Alignment
Alignment ist ein weiterer Prozess, bei dem die Bildverarbeitung zunehmend zum Einsatz kommt, neben den Prüfungen auf Menge und Vorhandensein von Teilen und Produkten, Aussehen (Fremdkörper, Werkstofffehler) und Abmessungen (Länge, Durchmesser). Bei der Alignment konnten sich Bildverarbeitungssysteme auf vielen Gebieten durchsetzen:
- Positionierung von Glassubstraten
- Messen auf Fehlausrichtung von Etiketten oder Strichcodes
- Prüfen der Ausrichtung von Mikrochips
- Prüfen auf falsch positionierte Deckel an Nahrungsmittelbehältern
- Positionskontrolle an Werkzeugmaschinen (per Bildverarbeitung gesteuerte Roboter)
In diesem Abschnitt werden die Grundprinzipien und spezifischen Anwendungen der Positionierung und Ausrichtung mittels Bildverarbeitung vorgestellt.
Grundprinzip der Ausrichtung und Positionserkennung mittels Bildverarbeitung
Schnelle und zuverlässige Positionierung
Um die Effizienz von Produktionsabläufen zu steigern, muss die relative Position zwischen Prüfobjekt und Werkzeugmaschinentisch ohne Verzögerung detektiert und das System entsprechend angesteuert werden. Mangelnde Genauigkeit bei der Erkennung kann zu Ausschuss führen. Jede zeitliche Verzögerung zwischen Erkennung und Ansteuerung kann zu Lasten der Produktivität gehen. Für die Automatisierungstechnik (FA) ist eine präzise Alignment unabdingbar. Die Bildverarbeitung wird in zunehmendem Maße eingesetzt, um dieser Herausforderung gerecht zu werden.
Probleme beim Alignment
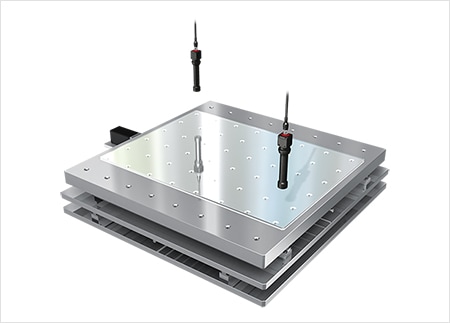
Bei der Herstellung von LCD-Bildschirmen müssen die Teile in einigen Prozessen, wie zum Beispiel der Glas- oder Folienlaminierung, sehr präzise positioniert werden. Auch wenn sich Bildverarbeitungssysteme in den letzten Jahren zunehmend durchgesetzt haben, gab es doch eine Reihe von Problemen:
- Das Positionieren mithilfe der Bildverarbeitung nahm zu viel Zeit bei der Kalibrierung in Anspruch.
- Der Prozess funktionierte wie eine Blackbox, daher war es schwierig, Funktionen hinzuzufügen, und dem Prozess selbst fehlte es an Vielseitigkeit.
- Expertenwissen war gefragt, um hohe Genauigkeit mit einer Positionierung in Hochgeschwindigkeit kombinieren zu können.
- Die beim Positionieren erreichte Genauigkeit war unzureichend, so dass die Einsatzmöglichkeiten beschränkt blieben.
Dank automatischer Kalibrierung und erhöhter Genauigkeit beim Postitionieren der Systeme, gehören diese Probleme der Vergangenheit an.
Ablauf der Positionierung auf Basis von Bildverarbeitungssystemen
Der erste wesentliche Schritt besteht darin zu verstehen, wie die Alignment auf Basis eines Bildverarbeitungssystems im Detail funktioniert. Je nach verwendetem System kann dieser Ablauf leicht variieren. Im folgenden Abschnitt soll das Grundprinzip der Positionierung anhand der KEYENCE Modellreihe XG-X am Beispiel der Glaslaminierung vorgestellt werden.
Automatische Kalibrierung
Mithilfe einer Mustersuche (Suchverarbeitung) o. Ä. wird die Position einer Ausrichtmarkierung ermittelt, auf deren Basis die Richtung der Objekttischachse und der Drehmittelpunkt berechnet werden.
Registrierung der Referenzposition
Die Position, auf die das zu prüfende Objekt transportiert wird, wird abgespeichert.
Ausrichtung
Die tatsächliche Position des Prüfobjekts wird vermessen und der Korrekturwert zur Referenzposition berechnet.
Positionierung
Die berechneten Positionsdaten werden an eine SPS oder ein anderes Hostsystem übermittelt und der Objekttisch auf die entsprechende Position verfahren.
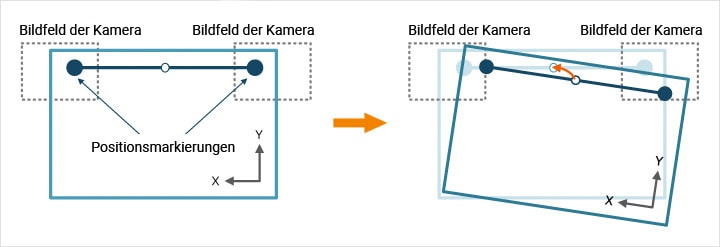
Vorteile der Positionierung auf Basis von Bildverarbeitungssystemen
Eine Implementierung von Bildverarbeitungssystemen für die Alignment bietet zahlreiche Vorteile:
Sehr präzise Positionserkennung durch Mustersuche
Die Mustersuche (Suchverarbeitung) ist für das Positionieren und Ausrichten mithilfe der Bildverarbeitung unverzichtbar. Mit ihr werden Referenzbilder oder Muster (Markierungen), die auch als Ausricht- oder Positionsmarkierungen bezeichnet werden, automatisch erkannt. Die Genauigkeit der Positionserkennung kann durch Korrektur der Objektivverzeichnung und den Einsatz von Filtern noch gesteigert werden.
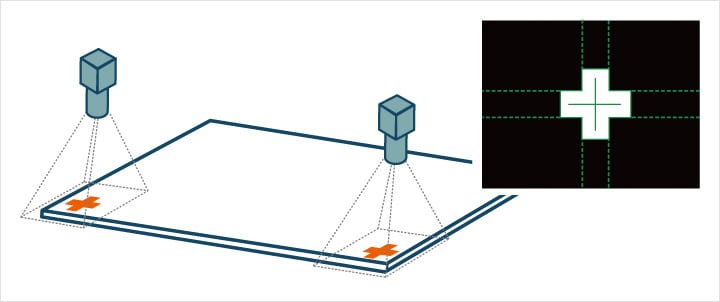
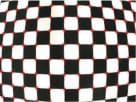
Vor der Korrektur

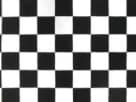
Nach der Korrektur
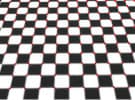
Vor der Korrektur

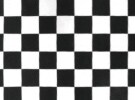
Nach der Korrektur
Automatische Kalibrierung zur Verbesserung der Taktzeiten
Bei der bisher verwendeten koordinatenbasierten Positionskontrolle kam es immer wieder zu Problemen, wie die Fehlausrichtung von Messobjekt und Tisch oder fehlende Erkennungsgenauigkeit, was eine ideale Erkennung von Position/Winkel verhinderte. In den letzten Jahren hat sich die Genauigkeit der automatischen Kalibrierung verbessert, was im Wesentlichen auf Fortschritte bei der Mustersuche zurückzuführen war. Diese Entwicklung führt zu sehr schnellen und hochpräzisen Kalibrierungen, welche die Taktzeiten deutlich verbessern.
Präzise Ansteuerung dank hochpräziser Erkennung auf Basis der Bildverarbeitung
Ausrichtmarkierungen können jetzt mithilfe von bildgebenden Verfahren mit sehr hoher Pixelzahl und verbesserten Bildverarbeitungstechnologien sehr präzise bestimmt werden. ShapeTrax ist die Suchtechnologie von KEYENCE, welche eine der branchenweit höchsten Genauigkeiten bietet. Mit ihr lassen sich Positionsgenauigkeiten von 0,025 Pixel sowohl hinsichtlich der Linearität als auch der Wiederholgenauigkeit erzielen.
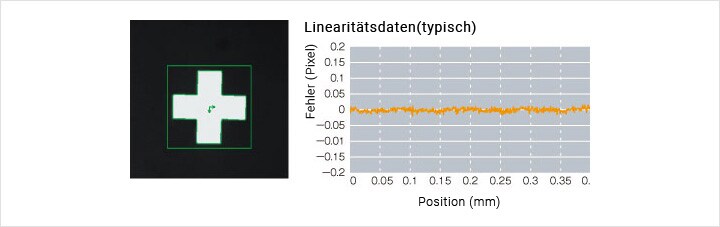
Neben der Suche nach Ausrichtmarkierungen kann die Positionserkennung je nach Einsatzfall auch flexibel und ohne Markierungen erfolgen. Zu den Methoden, die hier zum Einsatz kommen, gehören die Erkennung eines virtuellen Schnittpunkts an der Ecke einer Leiterplatte oder das Positionieren auf Grundlage einer Nut in einem Wafer.
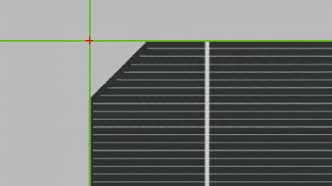
Erkennung eines virtuellen Schnittpunkts an der Ecke einer Leiterplatte
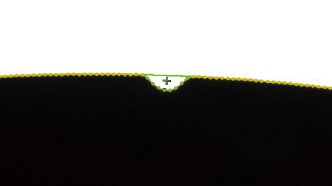
Positionierung auf Grundlage einer Wafer-Nut
Alignment mithilfe von Kameras mit sehr hoher Pixelzahl
KEYENCE bietet hochauflösende Kameras mit 21 Megapixel, welche zu den besten Lösungen der Branche zählen. Gängige Kameras mit geringeren Pixelzahlen wie 0,3 oder 2 Megapixel weisen die unten aufgeführten Probleme auf. Kameras mit sehr hoher Pixelzahl sind hier die erste Wahl.
Kommen Ihnen diese Probleme bekannt vor?
Produkte mit vielen Rundungen werden nicht sicher erkannt, weil keine zuverlässige Eckenerkennung möglich ist.
Herkömmlich
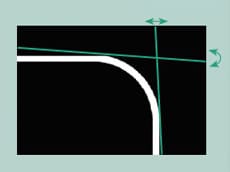
Ist die abgerundete Fläche sehr groß, ist der gerade Streckenabschnitt zu kurz, um die Ecke sicher erkennen zu können. Einige Produkte weisen keine Geraden auf, die für die Erkennung verwendet werden könnten.

Mit einer 21-Megapixel-Kamera wird ein Gesamtbild des Produkts aufgenommen
Von heute an
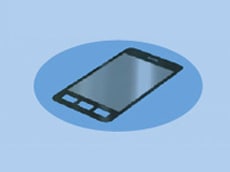
Ohne Abstriche bei der Genauigkeit kann ein das Produkt als Ganzes aufgenommen werden. Dadurch ist auch bei sehr komplex geformten Produkten eine hochpräzise Erkennung des gesamten Profils möglich.
Wird das Gesamtbild mit einer 21-Megapixel-Kamera aufgenommen, werden selbst komplexe Profile sehr präzise erkannt. Damit ist unabhängig von ihrer Form eine stabile und genaue Ausrichtung der Produkte gewährleistet.
Produktwechsel sind sehr arbeitsaufwändig, weil unterschiedliche Produkte in derselben Linie gefertigt werden.
Herkömmlich
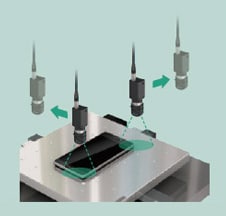
Die Abmessungen der Produkte ändern sich häufig. Layoutanpassungen bei jedem Produktwechsel sind arbeitsaufwändig.

Mit einer 21-Megapixel-Kamera wird ein Gesamtbild des Produkts aufgenommen
Von heute an
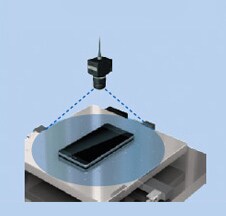
Bei einem Produktwechsel ist keine Änderung des Layouts erforderlich. Die Kamera bleibt in derselben Position, was den Ablauf vereinfacht.
Um die erforderliche Genauigkeit auch mit einer geringer auflösenden Kamera zu erreichen, muss das Bildfeld verkleinert werden. Wenn unterschiedliche Produkte in derselben Linie gefertigt werden, muss in der Folge das Layout der Kamera bei jedem Produktwechsel angepasst werden. Wird ein Gesamtbild des Produkts mit einer 21-Megapixel-Kamera aufgenommen, entfällt der Arbeitsaufwand für den Produktwechsel. Die Kamera kann in derselben Position bleiben, was den Produktionsprozess vereinfacht. Außerdem können zwei oder mehr Produkte gleichzeitig geprüft werden.
Qualitätskontrolle/ Dimensionsprüfungen mithilfe von Bildverarbeitung werden in einem von der Ausrichtung getrennten Prozess durchgeführt.
Herkömmlich
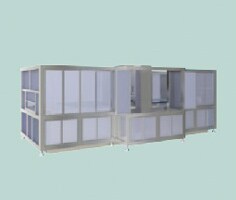
Die Prüfung von Abmessungen oder Qualitätsmerkmalen erfolgt in einem von der Ausrichtung getrennten Prozess. Dafür ist der Aufbau eines groß dimensionierten Systems erforderlich.

Mit einer 21-Megapixel-Kamera wird ein Gesamtbild des Produkts aufgenommen
Von heute an
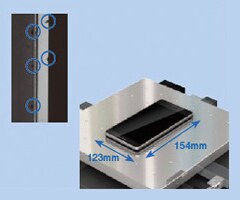
Die Prüfung von Abmessungen oder Qualitätsmerkmalen können am Produkt als Ganzes zeitgleich mit der Ausrichtung durchgeführt werden.
Es gibt immer noch viele Fälle, in denen die Prüfung von Abmessungen oder Qualitätsmerkmalen in einem von der Ausrichtung separaten Prozess abläuft. Wird das Bild eines Gesamtprodukts mit einer 21-Megapixel-Kamera aufgenommen, können Ausrichtung und Qualitätskontrolle am Gesamtprodukt gleichzeitig durchgeführt werden. Schlankere Fertigungsabläufe sind die Folge.
Praktische Anwendungen
Produkte müssen immer genauer gefertigt werden und dafür sind hochpräzise Prozesse erforderlich. Darüber hinaus gilt es, die Produktivität zu steigern, um den Ertrag zu erhöhen. Um diesen Anforderungen gerecht zu werden, besteht ein erhöhter Bedarf an Positionierungs- und Ausrichtungsprozessen, die sich der Vorteile der Bildverarbeitung bedienen. Im Folgenden möchten wir ein paar Implementierungsbeispiele vorstellen, bei denen die Bildverarbeitung und Kalibrierung erfolgreich eingesetzt wurde.
Erkennen von Führungsbohrungen bei der Karosseriemontage
Industrieroboter sind in Fertigungsprozessen wie dem Schweißen, beim Handling und in der Montage unabdingbar. Bisher war dafür ein umständliches Koordinaten-Teaching erforderlich, um Nullpunkte und Positionen einzulernen. Je nach Produkt oder individuellen Abweichungen waren unter Umständen noch Feinjustierungen erforderlich. Das Positionieren/Kalibrieren auf Basis von Bildverarbeitung ist eine mögliche Lösung für diese Probleme. Bei der Montage von Türen oder anderen schweren Teilen kann die Bildverarbeitung helfen, Führungsbohrungen zu finden und den Roboter zu steuern. Dadurch wird die Fertigung schneller und zuverlässiger. KEYENCE bietet außerdem Lösungen, um Industrieroboter per Bildverarbeitung zu steuern.
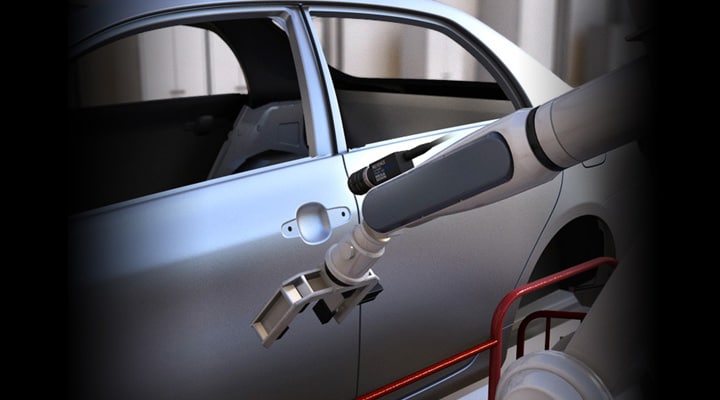
Fehlausrichtung von Mustern
Fehlausrichtungen im Mikrometerbereich an Wafern, die zur Herstellung von Halbleiterprodukten verwendet werden, können fatale Auswirkungen haben. Die Positionsdaten der Defekte müssen mithilfe von Instrumenten wie zum Beispiel optischen Mikroskopen ermittelt werden. Mit der Modellreihe XG-X und einer 21-Megapixel-Farbkamera lassen sich Fehlausrichtungen von Mustern oder Positionen wie die Drehrichtung von Wafern präzise erkennen.
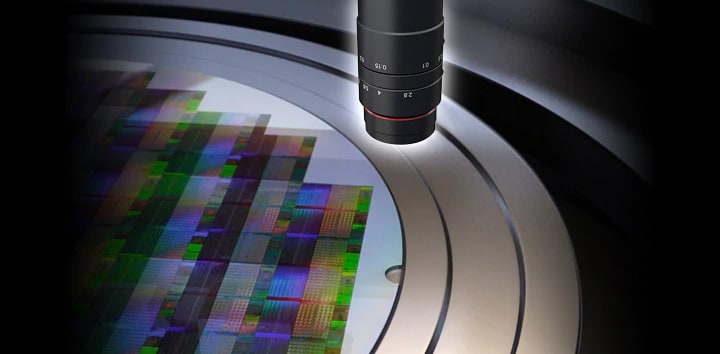
Montage von elektronischen Bauteilen
Da Smartphones und Tablets immer kompakter werden, nimmt auch die Notwendigkeit einer hohen Montagegenauigkeit in der Elektronikgeräteindustrie zu. Die Modellreihe XG-X unterstützt 21-Megapixel-Farbkameras mit einer hohen Auflösung und einem breiten Bildfeld, welche im Hinblick auf die Pixelanzahl ihres gleichen suchen. Damit werden detailgenaue Erkennungen von Mikrochips und hochpräzise Ausrichtungen möglich. Selbst winzigste Elektrobauteile lassen sich so präzise montieren.
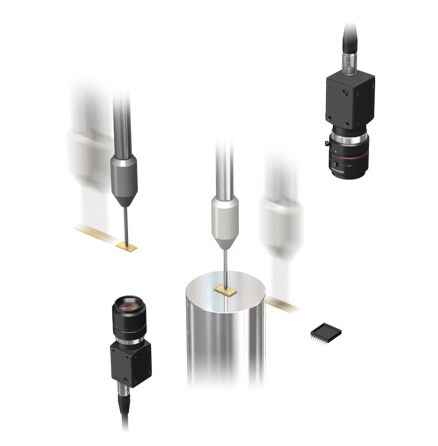
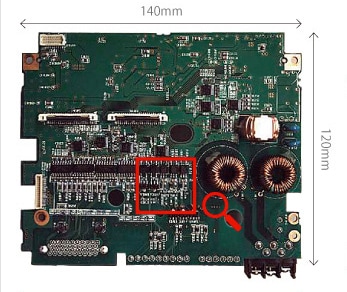
Vorteile einer 21-Megapixel-Kamera
Ein Großformatbild mit 21 Millionen effektiven Pixeln (5.104 x 4.092) kann mit 16-facher Geschwindigkeit in gerade einmal 110 ms übertragen werden. So können winzige Defekte bzw. Detailfehler in großen Messobjekten erkannt werden, was sich mit herkömmlichen Kameras bislang unmöglich war.

0,31 Megapixel
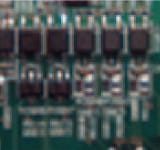
Das gesamte Bild ist verschwommen, und es ist nichts zu erkennen.
5 Megapixel
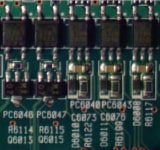
Die Profile der Chips sind verschwommen, eine präzise Erkennung ist schwierig.
21 Megapixel
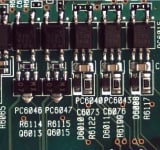
Jedes Detail ist gestochen scharf, so dass eine präzise Beurteilung möglich ist.