Dimensionsmessung
Dimensionsprüfungen sind ein Teilbereich der Prüfung von Qualitätsmerkmalen. Sie spielen eine wichtige Rolle bei der Unterscheidung zwischen Gutteil und Ausschuss bzw. bei der Entscheidung, ob Teile oder Produkte entsprechend den Vorgaben bearbeitet oder montiert wurden. Dimensionsprüfungen lassen sich mithilfe der Bildverarbeitung automatisieren:
- Messen der maximalen/ minimalen Abmessungen von Teilen oder Produkten
- Messen der maximalen/ minimalen/ durchschnittlichen Innen- oder Außendurchmesser bzw. Mittelpunktkoordinaten von O-Ringen
- Messen der Rundheit oder des Winkels an Spitzen von Metallteilen
- Messen der Position von Kanten und Etiketten
- Messen der Breite von Folienprodukten
Die Dimensionsmessung bildet die Grundlage der Prüfung; allerdings war sie bislang schwer zu implementieren, da sie viel Zeit und Aufwand bedeutete. Mit der aufkommenden Automatisierungstechnik hat auch der Einsatz von Dimensionsmessungen mithilfe der Bildverarbeitung zugenommen. Auf dieser Seite werden die Grundprinzipien, Vorteile und praktischen Anwendungsfälle von Dimensionsmessungen auf Basis der Bildverarbeitung vorgestellt.
Grundprinzip der Dimensionsmessung zur Überprüfung der Einhaltung von Spezifikationen
Vorteile der Einführung von Bildverarbeitungssystemen
Im Allgemeinen werden die Abmessungen von Teilen und Produkten mithilfe von Mikrometerschrauben und Messschiebern oder mithilfe von Messvorrichtungen kontrolliert, um sicherzustellen, dass keine Abweichungen hinsichtlich der Genauigkeit bestehen. Beim Messen mit diesen Instrumenten kommt es aber aufgrund der individuellen Unterschiede zwischen den Mitarbeitern und den Messbedingungen unweigerlich zu Fehlern. Das Ergebnis einer Prüfung mit einer Vorrichtung kann für die OK/N.i.O-Beurteilung herangezogen werden, um zu entscheiden, ob ein Produkt innerhalb des Toleranzbereichs liegt. Es liefert allerdings keine präzisen Messwerte.
Weitere Möglichkeiten für die Dimensionsmessung bieten Profilprojektoren, Konturographen und 3D-Messgeräte. Sie alle haben das Problem, dass sie aufgrund des erforderlichen manuellen Eingriffs zeitaufwändig und teuer sind.
Mithilfe der Bildverarbeitung lassen sich aus den vorhandenen Bildern gleich mehrere Abmessungen erfassen. Teile und Produkte können an unterschiedlichen Stellen vermessen werden. Anhand der Daten wird dann entschieden, ob sie innerhalb der Toleranz liegen. Ein weiterer Vorteil besteht darin, dass man Winkel oder die Rundheit von Kreisen zeitgleich mit den Längen einzelner Strecken messen und als numerische Daten abspeichern kann.
100%-Inspektion, damit keine Fehler übersehen werden und keine fehlerhaften Produkte das Werk verlassen
Die Dimensionsprüfung mithilfe unterschiedlicher Messsysteme und Vorrichtungen bringt in der Regel große Arbeitsumfänge außerhalb der Linie mit sich. Dementsprechend führen 100%-Inspektionen zu erheblichen Mehrkosten und einem größeren Personalaufwand. Wird dagegen nur in Stichproben geprüft, besteht die Gefahr, dass fehlerhafte Produkte das Werk verlassen. Bei Kombination der Dimensionsprüfung mit einem Bildverarbeitungssystem können sämtliche Werkstücke direkt in der Linie geprüft werden. Neben dem Vorteil gleichbleibender Produktqualität lassen sich so auch die Kosten niedrig halten.
Schnellere Prüfungen führen zu Produktivitätssteigerungen
Die Inline-Dimensionsmessung von Teilen und Produkten sorgt für eine signifikante Senkung der Prüfzeiten. Bildverarbeitungssysteme beschleunigen den Prüfprozess und steigern die Produktivität.
Speicherung und Verwaltung von Qualitätsdaten
Dimensionsprüfungen mit Vorrichtungen liefern keine genauen Messdaten. Es wird lediglich geprüft, ob eine Abmessung innerhalb des Toleranzbereichs liegt oder nicht. Dimensionsprüfungen mithilfe der Bildverarbeitung liefern nicht nur eindeutige OK/N.i.O-Ergebnisse, sondern auch numerische Daten bezüglich der präzisen Abmessungen zahlloser Prüfabschnitte, die einfach abgespeichert und verwaltet werden können. Diese Daten stehen nachfolgend für das Rückverfolgbarkeitsmanagement oder die Prozessoptimierung zur Verfügung.
Grundlagen der Dimensionsmessung: Messung auf Basis einer Kantenerkennung
Messungen anhand einer Kantenerkennung kommen häufig bei Dimensionsprüfungen mithilfe der Bildverarbeitung zum Einsatz. Im folgenden Abschnitt werden die Pixel-Auflösung, die Grundlagen der Subpixelverarbeitung und das Prinzip der Kantenerkennung erläutert.
Beziehung zwischen Bildauflösung und Beurteilungstoleranz
Das Bildaufnahmeelement eines Bildverarbeitungssystems besteht aus einer Anordnung von Punkten. Für die Dimensionsmessung kann man aufgrund der Anzahl dieser Punkte und des Bildfelds eine Abmessungstoleranz berechnen. Ein wichtiger Faktor für diese Berechnung ist die Pixel-Auflösung, unter der man die tatsächliche Länge eines einzelnen Bildpunkts des Bildaufnahmeelements versteht. Die Pixel-Auflösung wird anhand der folgenden Formel berechnet:
Pixel-Auflösung = Bildfeld in Y-Richtung [mm] / Anzahl der Punkte des Bildaufnahmeelements in Y-Richtung [Pixel]
Angenommen, Sie verwenden eine 0,31- und eine 2-Megapixel-Kamera. Die Anzahl der Punkte in Y-Richtung ist 480 für die 0,31-Megapixel-Kamera und 1.200 für die 2-Megapixel-Kamera.
Für ein Bildfeld von 100 mm bedeutet das:
- 【0,31 Megapixel】
- Pixel-Auflösung = 100 mm/480 Pixel = 0,208 mm/Pixel
- 【2 Megapixel】
- Pixel-Auflösung = 100 mm/1200 Pixel = 0,083 mm/Pixel
- 【21 Megapixel】
- Pixel-Auflösung = 100 mm/4092 Pixel = 0,024 mm/Pixel
Die Pixel-Auflösung kann auf diese Art und Weise berechnet werden. Die Tabelle unten enthält typische Pixel-Auflösungswerte von Kameras von 0,31 bis 21 Megapixel bei Einsatz in den gängigen Bildverarbeitungssystemen.
Pixel-Auflösung Referenzwert
Bildfeld (Y-Richtung)[mm] | |||||||||
---|---|---|---|---|---|---|---|---|---|
Pixelanzahl der Kamera | 1 | 5 | 10 | 20 | 30 | 50 | 100 | 200 | 500 |
0,31 Megapixel | 0.002 | 0.01 | 0.021 | 0.042 | 0.063 | 0.104 | 0.208 | 0.417 | 1.042 |
2 Megapixel | 0.0008 | 0.004 | 0.008 | 0.017 | 0.025 | 0.042 | 0.083 | 0.167 | 0.417 |
5 Megapixel | 0.0005 | 0.002 | 0.005 | 0.01 | 0.015 | 0.024 | 0.049 | 0.098 | 0.244 |
21 Megapixel | 0.0002 | 0.001 | 0.002 | 0.005 | 0.007 | 0.012 | 0.024 | 0.049 | 0.122 |
- * Anzahl der Punkte in Y-Richtung des CCD bei einem 0,31-Megapixel-Sensor = 480 Pixel
- * Anzahl der Punkte in Y-Richtung des CCD bei einem 2-Megapixel-Sensor = 1.200 Pixel
- * Anzahl der Punkte in Y-Richtung des CCD bei einem 5-Megapixel-Sensor = 2.050 Pixel
- * Anzahl der Punkte des Bildaufnahmeelements in Y-Richtung bei einer 21-Megapixel-Kamera = 4.092 Pixel
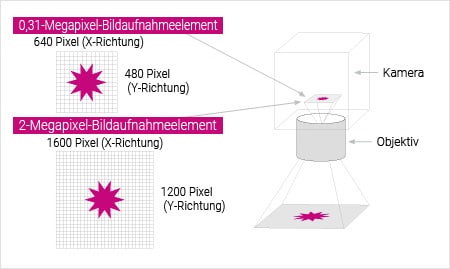
Bei der Dimensionsprüfung wird die Toleranz, die als Schwelle zur Unterscheidung von Gut- und Ausschussteilen verwendet wird, in der Regel in Einheiten von ±5 Pixel berechnet. Dafür geht man davon aus, dass die Anzahl der Punkte, mit der eine stabile Toleranzbeurteilung möglich ist, bei etwa dem 10-Fachen der Wiederholgenauigkeit liegt. Da die Wiederholgenauigkeit von typischen Bildverarbeitungssystemen im Idealfall etwa 0,1 Pixel beträgt, wird die Wiederholgenauigkeit einschließlich einer gewissen Toleranz in der Praxis auf 0,5 Pixel festgelegt. Multipliziert man diese Zahl mit 10, ergibt das ±5 Pixel. Dieser Wert kann als minimale Einheit für die Toleranzeinstellung angesehen werden. Anhand dieses Werts lässt sich die tatsächliche Maßtoleranz wie folgt berechnen:
Tatsächliche Maßtoleranz [mm] = Pixel-Auflösung (Bildfeld in Y-Richtung) [mm] / Anzahl der Punkte des CCD in Y-Richtung × 5 Pixel
- 【0,31 Megapixel】
- Maßtoleranz = 0,208 mm/Pixel × 5 Pixel = 1,04 mm
- 【2 Megapixel】
- Maßtoleranz = 0,083 mm/Pixel × 5 Pixel = 0,415 mm
- 【21 Megapixel】
- Maßtoleranz = 0,024 mm/Pixel × 5 Pixel = 0,12 mm
Bei der Auswahl eines Bildverarbeitungssystems und eines Bildfeld ist darauf zu achten, dass die erforderliche Genauigkeit damit erreicht werden kann.
Toleranz-Beurteilungswert Referenzwert
Bildfeld (Y-Richtung)[mm] | |||||||||
---|---|---|---|---|---|---|---|---|---|
Pixelanzahl der Kamera | 1 | 5 | 10 | 20 | 30 | 50 | 100 | 200 | 500 |
0,31 Megapixel | 0.01 | 0.05 | 0.1 | 0.2 | 0.3 | 0.5 | 1.0 | 2.1 | 5.2 |
2 Megapixel | 0.004 | 0.02 | 0.04 | 0.08 | 0.1 | 0.2 | 0.4 | 0.8 | 2.1 |
5 Megapixel | 0.002 | 0.01 | 0.02 | 0.05 | 0.07 | 0.1 | 0.2 | 0.5 | 1.2 |
21 Megapixel | 0.001 | 0.006 | 0.01 | 0.02 | 0.04 | 0.06 | 0.1 | 0.2 | 0.6 |

Grundlagen der Subpixelverarbeitung
Wie oben dargelegt, ist die Pixel-Auflösung der tatsächliche Abmessungswert eines einzelnen Bildpunkts. In der Praxis kann man bei einer Dimensionsmessung mit Bildverarbeitung durch eine Näherungsrechnung sehr wohl auch Abmessungen von weniger als einem Pixel darstellen. Dies wird auch als Subpixelverarbeitung bezeichnet.
Ein Subpixel ist eine Einheit, die kleiner als ein Pixel ist. Von KEYENCE angebotene Bildverarbeitungssysteme bieten zum Beispiel Maßangaben in einer Größenordnung von 1/1.000 Pixel.

Prinzip der Subpixelverarbeitung
Bei der Subpixelverarbeitung wird eine Kante als solche erkannt, wenn der Kontrast an einer Stelle zwischen Hell und Dunkel wechselt. Dieser Bereich wird in eine Projektionskurve umgewandelt, welche anschließend einer Differentialverarbeitung unterzogen wird. Der höchste Punkt der Differentialkurve wird als Kantenpunkt festgelegt.

Dimensionsmessung auf Basis einer Kantenerkennung
Wegen der hohen Pixel-Auflösung ist die Kantenerkennung vor allem für die Dimensionsmessung von besonderer Bedeutung. Im folgenden Abschnitt wird der grundlegende Ablauf der Kantenerkennung beschrieben.
1. Projektion
Um den durchschnittlichen Kontrast der Projektionslinie zu ermitteln wird das Messobjekt senkrecht zur Erkennungsrichtung abgetastet. Die Kurve des durchschnittlichen Kontrasts aus allen Projektionslinien wird als Projektionskurve bezeichnet.


2. Differenzierung
Bei genauer Ausdifferenzierung der Projektionskurve ergeben sich größere Differentialwerte für Punkte, bei denen es sich um Kanten handeln könnte. Unter Differenzierung versteht man einen Prozess, mit dem Änderungen im Kontrast (Kontraststufen) ermittelt werden.
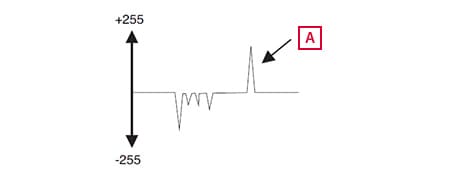
Differentialkurve (Kantenintensitätskurve)
3. Anpassung des maximalen Differentialwerts auf 100%
Die Kurve wird so korrigiert, dass der maximale Differentialwert und der Absolutwert 100% betragen, um die Kante zu stabilisieren. Der höchste Punkt der Differentialkurve, der die vorgegebene Kantenempfindlichkeit übersteigt, wird als einer der Kantenpunkte festgelegt.
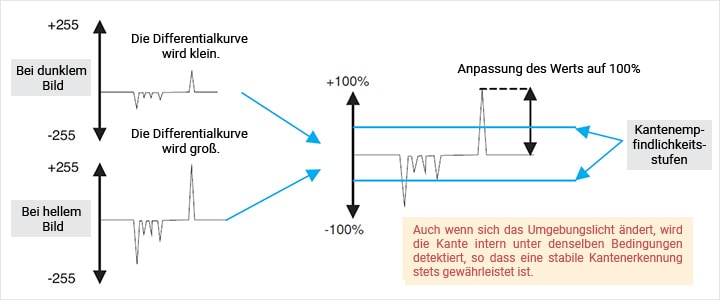
4. Subpixelverarbeitung
Berechnet wird die Kurve für drei Punkte, dem höchsten innerhalb der Differentialkurve und zwei benachbarte Punkte, und anschließend die Kantenposition in Einheiten von 0,001 Pixel gemessen.
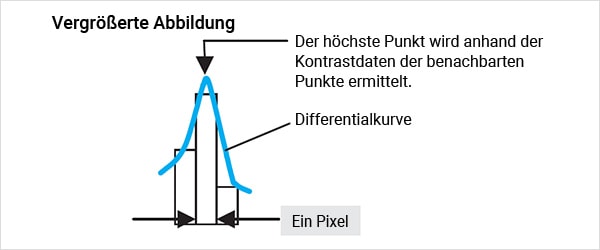
Praktische Anwendungen
Im Zuge der zunehmenden Automatisierungstechnik ist die Zeitersparnis bei der Qualitätskontrolle eine der wesentlichen Herausforderungen, dasselbe gilt auch für die Dimensionsmessung. Der Einsatz der Bildverarbeitung beim Messen ist zu einer der Schlüsseltechnologien für diese Art der Prozessoptimierung geworden.
Prüfung von mehreren Abmessungen an Chip-Kondensatoren
Zusätzlich zu Durchmesser und Länge des Kondensatorgehäuses lassen sich seine Teile in Segmente aufteilen, an denen eine Kantenpositionserkennung durchgeführt werden kann, um den minimalen Durchmesser eines sich verjüngenden Bereichs bzw. die Länge oder Biegung eines Anschlussdrahts zu ermitteln. Die Abmessungen jedes einzelnen Teils können präzise erfasst werden.

Prüfbildschirm


Dimensionsmessung an Flaschenhälsen
Abmessungen können auch direkt an der Linie präzise gemessen werden. Anhand eines Bilds von einer PET-Flasche, das auf einem sich bewegenden Transportband von der Seite aus aufgenommen wird, kann man beispielsweise die Abmessung des Flaschenhalsrings messen, um defekte Formteile, falsche Teiletypen oder Montagefehler zu erkennen. Mit dieser Art der Inline-Prüfung lässt sich die Effizienz steigern.

Prüfbildschirm
