Automobilkarosserie

Ein Automobil besteht aus vielen verschiedenen Komponenten. Während Elektrofahrzeuge und vernetzte Autos in den letzten Jahren zu einem beliebten Gesprächsthema geworden sind, war die Reduzierung des Karosseriegewichts eine Herausforderung vor dem Hintergrund der Forderungen nach Reduzierung der Umweltbelastung und Verbesserung der Kraftstoffeffizienz. Dies gilt auch für Fahrzeugkomponenten wie Sekundärbatterien, Steuergeräte und Stecker.
Als Technologie zur Erfüllung dieser Anforderungen ist die Klebe- und Filmbildungsbeschichtung zu einer beliebten Option bei Prozessen im Karosseriebau geworden.
- Verklebung in der Automobilindustrie (Karosseriebau)
- Funktionalisierung und Oberflächenbearbeitung in der Automobilindustrie (Karosseriebau)
Verklebung in der Automobilindustrie (Karosseriebau)
- Strukturkleber (Schweißkleben)
- Schweißkleben ist ein hitzig diskutiertes Thema in der Karosseriemontage geworden. Diese Technologie kombiniert Punktschweißen für Kontaktpunkte und Strukturkleber (Schweißkleben) für Kontaktflächen. Mit diesem Verfahren kann die Anzahl der Schrauben und anderen Teile sowie die Anzahl der für das Schweißen erforderlichen Arbeitsstunden reduziert und gleichzeitig eine leichte und doch hochfeste Verbindung erreicht werden. Darüber hinaus schafft die reduzierte Anzahl von Schweißpunkten eine hohe Wertschöpfung für den Karosseriebau, wie z. B. flexiblere Karosseriekonstruktionen.
Thema: Multimaterialproduktion zur Reduzierung des Karosseriegewichts
Die Reduzierung des Karosseriegewichts ist zu einem wichtigen Thema geworden, damit Umweltauflagen erfüllt und die Kraftstoffeffizienz verbessert werden können. Um dieses Ziel zu erreichen, hat der Einsatz von Verbundwerkstoffen aus CFK (Kohlefaserverstärkter Kunststoff) in Verbindung mit Aluminiumlegierungen oder Magnesiumlegierungen in Europa und Japan zugenommen.
Das direkte Fügen durch Reibungswärme unter Ausnutzung der Thermoplastizität (die Eigenschaft eines Materials, das beim Erwärmen weich wird) von CFK wurde als Methode zum Verbinden ungleicher Werkstoffe untersucht. Aufgrund der unterschiedlichen Wärmeausdehnungsverhältnisse bleiben einige Herausforderungen bestehen, wie z. B. der Festigkeitserhalt in einer Fahrumgebung und die Korrosionsbeständigkeit des verbundenen Teils. Die Kombination aus Beschichtung mit einem leichten, hochfesten Strukturkleber und Einsatz von Schrauben ist ein derzeit effektives Fügeverfahren.
Thema: Automatische Beschichtung von Dichtstoffen (Versiegelung, Grundierung) bei der Montage von Glasscheiben
Bei der Montage von Glasscheiben an Karosserien wird ein Dispenserroboter zur automatischen Beschichtung von Dichtstoffen (Versiegelung, Grundierung) eingesetzt. Wenn die Versiegelung unsachgemäß beschichtet wird, können Wasser und andere Fremdkörper in das Innere eindringen und die Korrosionsbeständigkeit des Körpers beeinträchtigen.
Die Dichtmasse muss kontinuierlich und in geeigneter Form (Höhe, Breite und Volumen) über den gesamten Umfang aufgetragen werden. Um die Freigabe fehlerhafter Messobjekte zu verhindern, ist es notwendig, die Form der Dichtungsmasse in Echtzeit zu messen, indem man die automatische Beschichtung verfolgt.
Funktionalisierung und Oberflächenbearbeitung in der Automobilindustrie (Karosseriebau)
Die Reihe der Beschichtungsprozesse im Karosseriebau umfasst die Beschichtung nicht nur zu Konstruktionszwecken, sondern auch zur Funktionserweiterung der Karosserieoberfläche. Eine typische beschichtete Karosserieoberfläche weist folgende Schichten auf:
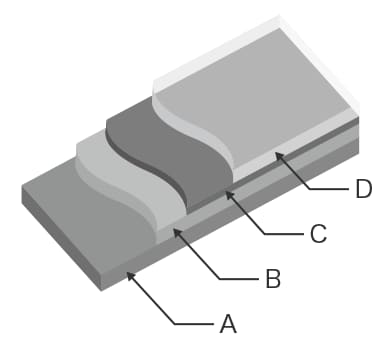
- Elektrotauchlackierungsschicht (A)
- Diese Schicht fügt eine Rostschutzfunktion hinzu. Meist wird die Tauchlackierung (Immersion) eingesetzt.
- Zwischenschicht (B)
- Durch die Funktion dieser Schicht werden Absplitterungen verhindert. Diese Funktion verhindert, dass der Grundstahl durch Steinschläge oder andere Ereignisse freigelegt wird.
- Grundierung (C)
- Diese Schicht fügt Farbe für Konstruktionszwecke hinzu. Je nach Konstruktionszweck können mehrere Prozesse eingesetzt werden.
- Klarlack (D)
- Der Zweck dieser Schicht ist es, die Haltbarkeit zu verbessern, z. B. beim Oberflächenschutz und bei der Wetterbeständigkeit.
Anders als bei der Ablagerungsschicht setzen Karosseriebeschichtungsverfahren elektrostatische Lackierung mit Lackierrobotern ein. Die Lackierroboter wurden technisch immer ausgereifter, wie z. B. bei mehrachsigen Strukturen sowie mit ihrer Fähigkeit, auf kleinstem Raum zu lackieren und automatischen Werkzeugwechsel vorzunehmen.
Zusatzinformationen: Aktueller Stand der Lackierroboter
Thema: Schwingungsdämpfende Beschichtung zur Verbesserung von Effizienz und Funktionalität
Auf Karosserieböden werden schwingungsdämpfende Materialien verwendet, um Schwingungsgeräusche zu reduzieren und die Laufruhe in der Kabine zu verbessern. Bisher eingesetzte Verfahren beinhalten das manuelle Schneiden und Kleben eines Werkstoffbogens. In den letzten Jahren wurden solche Verfahren jedoch durch die Beschichtung mit schwingungsdämpfenden Materialien ersetzt, um Effizienz und Funktionalität zu verbessern.
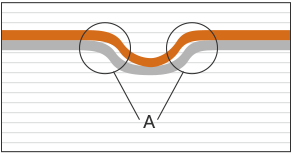
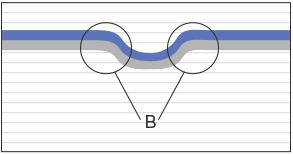
- A. Lücken, die die Leistung beeinträchtigen
- B. Perfekte Haftung, die die Leistung verbessert
Die Verwendung von bogenförmigem Material stellt auch ein Problem im Hinblick auf geringere schwingungsdämpfende Eigenschaften dar, da Lücken entstehen, wenn der Bogen auf unebenen oder abgerundeten Oberflächen aufgebracht wird.
Andererseits kann Beschichtungsmaterial mit einem Dispenserroboter, der in der Lage ist, die Beschichtung auch in einem Winkel gleichmäßig aufzubringen, automatisch und mit hoher Genauigkeit beschichtet werden. Solche Roboter können den Prozess verkürzen, Arbeit sparen und Materialverluste reduzieren. Die Verklebung gewährleistet eine zuverlässige Beschichtung in der erforderlichen Menge bei vollständigem Kontakt mit der Oberfläche, unabhängig davon, ob sie uneben oder gekrümmt ist. Dadurch erreicht man eine Leichtbauweise mit hoher Schwingungsdämpfung.
Für die automatische Beschichtung mit einem Dispenserroboter ist es wichtig, die Formprüfung zur Vermeidung von Beschichtungsfehlern unmittelbar nach der Beschichtung durch Verfolgen der Dispenserdüse durchzuführen.
Referenzbeispiel: Beschichtungsprüfung von Automobilkomponenten