Messung von Verschleiß
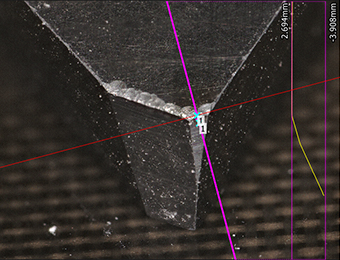
Verschleiß tritt an den Kanten von Werkzeugen oder den Gleitflächen von mechanischen Bauteilen auf und hat einen großen Einfluss auf die Leistung. Die Auswirkungen von Verschleiß können zu Bearbeitungsfehlern (aufgrund von Hitze oder Vibrationen), Betriebsfehlern (aufgrund von Lockerheit) und im schlimmsten Fall zu Fehlfunktionen oder Schäden an der Maschine führen.
Öl oder andere Schmiermittel können verwendet werden, um Verschleiß zu minimieren. Es ist jedoch schwierig, Verschleiß vollständig zu verhindern, deshalb bleibt er ein potenzieller Risikofaktor. Aus diesem Grund ist die Messung von Verschleiß unerlässlich, um die Produktqualität zu erhalten, die Geräte zu warten und die Sicherheit zu gewährleisten.
- Verschleiß
- Arten von Verschleiß
- Notwendigkeit der Verschleißmessung
- Herausforderung bei gängigen Messungen von Verschleiß
- Lösungen für Herausforderungen bei der Messung von Verschleiß
- Zusammenfassung: Erhebliche Verbesserung und höhere Effizienz bei komplexen Verschleißmessungen
Verschleiß
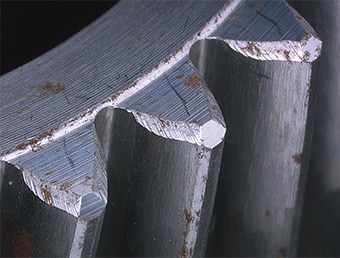
Verschleiß tritt auf, wenn das Material einer festen Oberfläche infolge von Reibung allmählich abgetragen wird. Reibung und Verschleiß werden sowohl von externen Faktoren (wie Belastung, Geschwindigkeit, Temperatur und Atmosphäre) als auch von technischen Faktoren (wie geometrischer Form, Verformung und Zustand der Schnittstellen) beeinflusst.
Erosion ist dem Verschleiß ähnlich und bezieht sich auf die Abnutzung, die durch Reibung zwischen einer Flüssigkeit und einem festen Gegenstand entsteht. Erosion kann zum Beispiel zwischen der Flüssigkeit in einem Rohr und den Rohrwänden auftreten.
Arten von Verschleiß
Verschleiß ist das Ergebnis einer sehr großen Anzahl von Parametern, die auf komplexe Weise zusammenwirken. Dazu gehören der Ort der Reibung, die physikalischen Eigenschaften der Reibmaterialien, die Umgebungsbedingungen, Hitze, Temperaturschwankungen sowie physikalische und chemische Einwirkungen. In diesem Abschnitt werden einige gängige Arten von Verschleiß vorgestellt.
Adhäsiver Verschleiß
Adhäsiver Verschleiß tritt auf, wenn zwei feste Objekte aneinander reiben und miteinander verbunden (verklebt) werden, dann brechen und sich trennen. Adhäsiver Verschleiß entsteht durch chemische Bindungen zwischen den festen Gegenständen. Aus diesem Grund ist ein Adhäsiver Verschleiß zwischen den folgenden Arten von festen Gegenständen wahrscheinlich:
- Materialien der gleichen Art
- Materialien, die die gleiche kristalline Struktur und ähnliche Gitterkonstanten haben
Abrasiver Verschleiß
Abrasiver Verschleiß tritt zwischen zwei festen Objekten auf, wenn die Vorsprünge des härteren Materials das weichere Material mechanisch abtragen. Zu den Merkmalen gehören vergleichsweise gute Schmierungsbedingungen und ein geringer Grad an Adhäsion sowie ein größerer Verschleiß im Vergleich zu anderen Verschleißarten.
Ermüdungsverschleiß
Ermüdungsverschleiß tritt auf, wenn die Rollreibung gegenüber der Gleitreibung überwiegt, z. B. auf der Lauffläche eines Lagers oder auf der Oberfläche eines Zahnrads. Der Prozess, der zur Ermüdungsreibung und demnach zum Verschleiß führt, ist wie folgt:
- (1) An der Oberfläche, an der sich Metallteile berühren, wirken wiederholte Belastungen.
- (2) Diese wiederholten Belastungen führen dazu, dass sich die Oberfläche allmählich verhärtet.
- (3) Es entstehen feine Risse, die sich zu größeren Rissen entwickeln.
- (4) Die Oberflächenschicht schält sich ab.
Die Scherspannung, die die feinen Risse in (3) verursacht, ist an einem Punkt leicht unterhalb der Oberfläche am höchsten. Derselbe Prozess wie oben führt auch zu Lochfraß, der als Folge von Rollermüdung fleckenartige Vertiefungen auf einer Lageroberfläche bildet, sowie zu Splittern, bei denen als Folge von Materialermüdung beträchtlich große Metallfragmente von der Zahnoberfläche abfallen.
Fressverschleiß
Fressverschleiß ist ein Verschleiß, der an der Kontaktfläche zwischen Materialien auftritt, die in der Annahme konstruiert wurden, sie würden nicht verrutschen. Wenn Bauteile, die mit Schrauben und Muttern befestigt sind (oder die Kontaktflächen zweier Bauteile), wiederholt belastet werden, kommt es zu einem leichten relativen Abrutschen (Fressen), das Verschleiß verursacht. Feine Risse entstehen an der Oberfläche, an der sich Fressverschleiß bildet. Da die äußere Belastung und die wiederholte Beanspruchung auf die Stelle des Fressverschleißes einwirken, wird die Dauerfestigkeit auf die Hälfte oder weniger des ursprünglichen Wertes reduziert, was zu einem Ermüdungsbruch führt.
Notwendigkeit der Verschleißmessung
Der Verschleiß von Bearbeitungswerkzeugen steht in direktem Zusammenhang mit der Bearbeitungsqualität, und der Verschleiß von Bauteilen steht in direktem Zusammenhang mit der Betriebsgenauigkeit und Sicherheit. Aus diesem Grund ist es äußerst wichtig, die Verschleißbedingungen zu messen, z. B. den Verschleißgrad. In diesem Abschnitt wird die Bedeutung der Verschleißmessung am Beispiel eines Bremsbelags und eines Schneidwerkzeugs erläutert.
Verschleißmessung von Bremsbelag
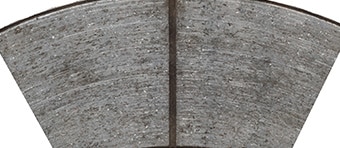
Ein neuer Autobremsbelag ist etwa 10 mm dick. Obwohl der Zeitpunkt je nach Hersteller variiert, wird der Bremsbelag im Allgemeinen ausgetauscht, wenn er auf etwa 1 bis 3 mm abgenutzt ist. Der Bremsbelag wird bei einer Scheibenbremse durch die Reibung mit der Bremsscheibe und bei einer Trommelbremse durch die Reibung mit der Bremstrommel abgenutzt. Auch die Bremsscheibe und die Bremstrommel werden abgenutzt. Da die Verschleißerscheinungen auf der abgenutzten Oberfläche des Bremsbelags zu sehen sind, können die Haltbarkeit des Bremsbelags und die Art der Abnutzung beim Bremsen durch Messung oder Betrachtung des Bremsbelagvolumens und des Verschleißgrads ermittelt werden.
Verschleißmessung von Drehwerkzeugen
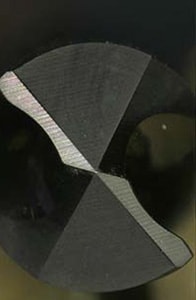
Die Spitze eines Schaftfräsers oder eines Drehmeißels wird durch die Reibung mit dem Werkstück und den Spänen abgenutzt. Die Teile, die sich abnutzen, sind je nach Material unterschiedlich. In den meisten Fällen tritt der Verschleiß jedoch an der Spanfläche und der Entlastungsfläche auf. Mögliche Ursachen sind eine zu hohe Schnittgeschwindigkeit oder ein ungeeignetes Material des Drehwerkzeugs. Da die Belastung des Werkzeugs bei der Bearbeitung eines schwer zerspanbaren Materials zunimmt, ist der Verschleiß größer als bei der Bearbeitung normaler Materialien. Es ist Vorsicht geboten, da die Reibung an der Entlastungsfläche die Schnittkraft erhöhen oder die Schnitttiefe verändern kann.
Aus diesen Gründen ist die Verschleißmessung von Drehwerkzeugen äußerst wichtig für die Bewertung der Schnittgeschwindigkeit und die Auswahl des Werkzeugmaterials.
Herausforderung bei gängigen Messungen von Verschleiß
In der Regel wird der Verschleiß mit Profilmesssystemen oder 3D-Koordinatenmessgeräten gemessen. Bei diesen Methoden treten jedoch die folgenden Herausforderungen bei der Verschleißmessung auf einer großen Fläche oder an kleinen Bauteilen auf.
Herausforderung bei der Messung von Verschleiß mit einem Profilmesssystem
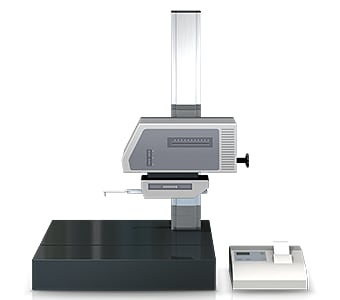
Ein Profilmesssystem oder Konturograph misst und erfasst das Profil eines Messobjekts, indem es dessen Oberfläche mit einem Taststift nachfährt. In den letzten Jahren wurden Profilmesssysteme entwickelt, die mit einem Laser anstelle eines Taststifts komplexe Formen messen, indem sie das Profil berührungslos verfolgen. Einige Modelle sind sogar in der Lage, Messungen sowohl der Ober- als auch der Unterseite durchzuführen.
Ein Profilmesssystem muss eine genaue Messlinie für den Verschleißgrad am Messobjekt ziehen.
Dies beinhaltet die folgenden Herausforderungen:
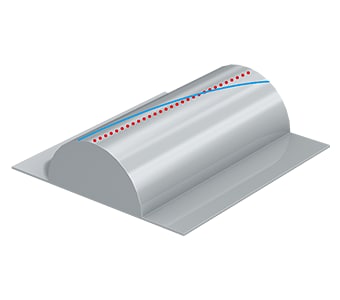
- Die Messung erfordert viel Zeit, einschließlich der Zeit für die Befestigung der Probe auf der Vorrichtung und deren Nivellierung. Es sind zudem Kenntnisse und Fähigkeiten im Umgang mit Profilmesssystemen erforderlich, um ein Messobjekt genau zu nivellieren.
- Der Taststift eines Profilmesssystems bewegt sich in einem Bogen auf und ab, der auf dem Drehpunkt des Tastarmes zentriert ist, und die Tastspitze bewegt sich auch in Richtung der X-Achse, was zu Fehlern in den Daten der X-Achse führt.
- Das Nachzeichnen der gewünschten Linie mit dem Taststift ist eine äußerst schwierige Arbeit, und selbst eine leichte Verschiebung des Taststifts führt zu Fehlern in den Messungen.
- Es ist auch schwierig, die Anzahl der Messobjekte zu erhöhen, weil man bestimmte Positionen für die Messung festlegen muss.
- Es kann nur ein Teil eines Messobjekts gemessen werden, und die Auswertung der gesamten Oberfläche ist nicht möglich.
Herausforderung bei der Messung mit einem 3D-Koordinatenmessgerät
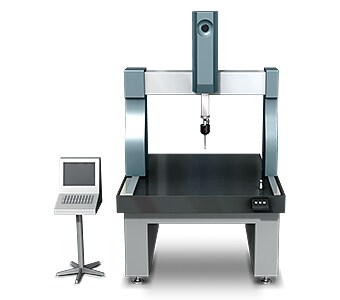
Wenn die Fläche des abgenutzten Bauteils klein ist, zum Beispiel 1 mm2, ist es sehr schwierig, die Form genau zu messen, indem man die Oberfläche mit einem Messtaster anvisiert und eine virtuelle Oberfläche erstellt. Auch bei der Messung einer kleinen Fläche ist es aufgrund der geringen Anzahl von Messpunkten schwierig, die genaue 3D-Form zu ermitteln. Viel Arbeit machen auch die damit verbundenen Aufgaben, wie z. B. die tabellarische Erfassung der Messdaten und der Vergleich der Ergebnisse mit den Zeichnungen.
Lösungen für Herausforderungen bei der Messung von Verschleiß
Gängige Messgeräte messen ein dreidimensionales Messobjekt oder eine Fläche mittels Punkt- und Linienkontakt. Dies führt zu Herausforderungen, da nicht die gesamte Form erkannt werden kann und die Zuverlässigkeit der gemessenen Werte gering ist. Um diese Messprobleme zu lösen, hat KEYENCE das 3D-Profilometer der Modellreihe VR entwickelt.
Die Modellreihe VR erfasst präzise die 3D-Form der gesamten Oberfläche, ohne das Messobjekt zu berühren. Die 3D-Form kann zudem durch einen 3D-Scan des Messobjekts in nur einer Sekunde mit hoher Präzision gemessen werden. Das System ist in der Lage, sofortige und quantitative Messungen durchzuführen, ohne fehlerhafte Messergebnisse zu erhalten. In diesem Abschnitt werden einige Vorteile der Modellreihe VR vorgestellt.
Vorteil 1: Datenerfassung der gesamten Oberfläche innerhalb von Sekunden
Die Modellreihe VR misst die gesamte Oberflächenform und erfasst dabei hunderttausende Messpunkte. Da die Messung nicht anhand von Linien oder Punkten erfolgt, ist eine Wiederholung der Messung nicht erforderlich, wodurch die Messzeit verkürzt wird. Elemente, die schwer zu definieren sind, wie z. B. der Verschleißgrad, können anhand des Volumens oder der Oberfläche bewertet werden. Es ist auch möglich, eine einfache quantitative Bewertung der Ebenheit durchzuführen. Die Modellreihe VR kann auch Profilmessungen an bestimmten Orten durchführen. Auch nach der Messung können Profile an verschiedenen Stellen aus den 3D-Scandaten erfasst werden, ohne das Messobjekt erneut zu scannen.
Alle Messdaten werden gespeichert und die gespeicherten Daten können mit CAD-Daten oder anderen Messdaten verglichen werden.
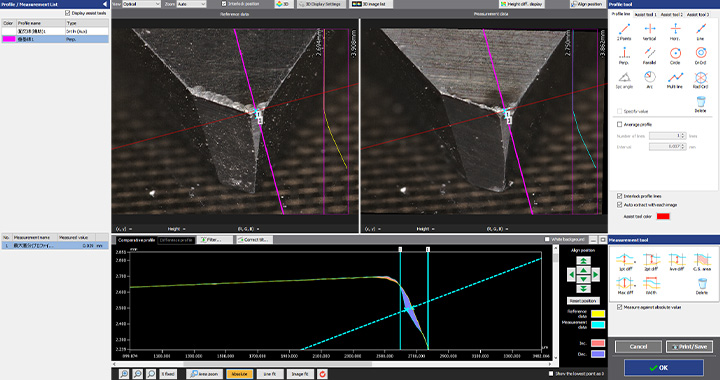
Vorteil 2: Messungen großer Flächen von bis zu 300 mm x 150 mm sind möglich
Für die Messung legen Sie das Messobjekt auf den Objekttisch und starten Sie die Aufnahme. Eine genaue Positionierung oder sonstige Vorbereitung ist nicht erforderlich. So können auch hochpräzise Messungen durch Anwender, die über keine Kenntnisse oder Erfahrungen im Umgang mit Messgeräten verfügen, durchgeführt werden.
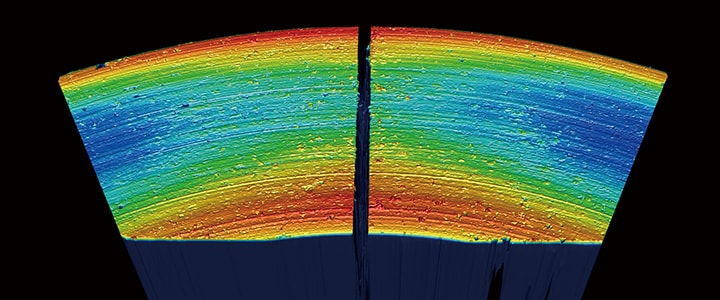
Da die Modellreihe VR die Merkmale des Messobjekts auf dem Objekttisch extrahiert und seine Position automatisch korrigiert, ist eine genaue Positionierung, die viel Zeit und Mühe erfordert, nicht erforderlich. Die Modellreihe VR kann auch einen großen Bereich von bis zu 300 mm x 150 mm messen, indem sie mehrere Messbilder zusammenfügt. So können auch unerfahrene Anwender einfach und sofort Messungen durchführen. Es muss kein Fachpersonal beauftragt werden.
Mit der Modellreihe VR kann kann eine große Fläche, z.B. ein großer Bremsbelag, präzise gemessen werden.
Zusammenfassung: Erhebliche Verbesserung und höhere Effizienz bei komplexen Verschleißmessungen
Die Modellreihe VR kann 3D-Messobjekte präzise und sofort mit hoher Geschwindigkeit messen, ohne das Messobjekt zu berühren. Das System löst alle Herausforderungen, mit denen handelsübliche Messgeräte konfrontiert sind, indem es die Messung der höchsten und niedrigsten Punkte auf der Verschleißoberfläche sowie die Messung des Volumens, der Querschnittsfläche und des Verhältnisses von Oberfläche zu Querschnittsfläche ermöglicht.
- Es ist in der Lage, gleichzeitig den höchsten Punkt, den tiefsten Punkt, die Fläche, das Volumen und die Oberfläche genau zu messen.
- Dies verhindert durch menschliche Faktoren bedingte Abweichungen und ermöglicht so eine zuverlässige quantitative Messung.
- Es sind weder Positionierung noch andere Vorbereitungen erforderlich. Anwender können einfach das Messobjekt auf den Objekttisch platzieren und die Aufnahme per Klick starten. Damit muss für die Messung kein Fachpersonal mehr herangezogen werden.
- 3D-Formen können mit hoher Geschwindigkeit und Präzision gemessen werden. Dadurch ist es möglich, eine große Anzahl von Messobjekten in kurzer Zeit zu messen, was zur Qualitätsverbesserung beiträgt.
Dieses System ermöglicht auch Vergleiche mit früheren Messdaten und CAD-Daten sowie eine einfache Datenanalyse, wie z. B. die Verteilung innerhalb der Toleranzen. Es kann effektiv für eine Vielzahl von Zwecken eingesetzt werden, einschließlich Produktentwicklung, Trendanalysen in der Produktion und Stichprobenprüfungen.