Messung von Oberflächen
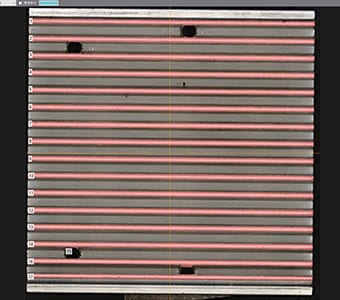
Messungen an der Oberfläche eines dreidimensionalen Objekts, wie eines Würfels, einer Kugel oder eines Kegels sind mit einem hohen Schwierigkeitsgrad verbunden. Häufig werden dafür optische Mikroskope, Digitalmikroskope oder CNC-Bildmessgeräte verwendet. Mit diesen Werkzeugen können Sie die Oberfläche zwar erfassen, aber das Sichtfeld ist meist stark begrenzt. Obwohl die Messung mit einem Wegmesssensor oder einem Rauheitsmessgerät möglich ist, messen diese Geräte nur Punkte und Linien, was viel Arbeit und Zeit für die Messung der Oberfläche erfordert.
Im Folgenden werden die Oberflächen verschiedener Messobjekte, Herausforderungen bei der Messung sowie geeignete Lösungsvorschläge vorgestellt.
- Oberfläche
- Herausforderung bei gängigen Oberflächenmessungen
- Lösungen für Herausforderungen bei der Oberflächenmessung
- Zusammenfassung: Erhebliche Verbesserung und höhere Effizienz bei komplexen Oberflächenmessungen
Oberfläche
Der Begriff „Oberfläche“ bezieht sich auf die Fläche einer 3D-Form. Die Erfassung der Oberfläche ist wichtig bei der Bewertung der Funktionalität, zusammen mit Textur, Haftung, Gleitfähigkeit, Wärmeableitung und Oberflächenrauheit. Bei Metallbruch- oder Reibungsflächen, PGAs oder Gravuren mit einem Beschriftungslaser kann die Messung der Oberfläche beispielsweise eine Vielzahl von Informationen liefern.
Metallbruchfläche
Durch eine detaillierte Betrachtung der Metallbruchfläche kann die Ursache des Bruchs anhand der Bruchmorphologie bis zu einem gewissen Grad identifiziert werden. Die Messung ermöglicht auch die Berechnung von Merkmalen wie dem prozentualen Anteil des duktilen Bruchs, der den Anteil des Sprödbruchs an der gesamten Bruchfläche angibt.
Verschleißfläche
Da die Oberflächen aller festen Gegenstände rau oder wellenförmig sind, ist selbst der Kontakt zwischen nominell ebenen Oberflächen in Wirklichkeit ein Kontakt zwischen Vorsprüngen, die sich auf den Oberflächen befinden (auch als tatsächliche Kontaktfläche bezeichnet). Die Messung der Verschleißfläche ermöglicht es, die Ursache des Verschleißes zu ermitteln. Die tatsächliche Kontaktfläche kann anhand der Oberfläche und der Rauheit der Verschleißfläche berechnet werden, wodurch sich die Verschleißbedingungen leicht ermitteln lassen.
PGA-Oberfläche
PGAs (Pin Grid Arrays) sind eine der Arten von IC-Gehäusen. Da die Pins in hoher Dichte in Buchsenleisten eingesetzt werden, ist es unmöglich, das PGA in der Buchsenleiste zu montieren, wenn es Abweichungen in der Dicke, der Höhe oder dem Winkel der Pins gibt. Aus diesem Grund ist es wichtig, Merkmale wie die Höhe der Pins, das Volumen und die Oberfläche an einer großen Anzahl von Stellen zu messen.
Oberfläche einer durch einen Beschriftungslaser erzeugten Gravur
Die Qualität der durch einen Beschriftungslaser erzeugten Gravur kann durch Messung des Volumens, der Oberfläche und der Querschnittsfläche des gravierten Teils beurteilt werden. Diese Werte können bei der Einstellung der Laserbestrahlungsintensität, des Laserlicht-Absorptionsvermögens des Materials, des Lichtpunktdurchmessers und anderer Parameter hilfreich sein.
Herausforderung bei gängigen Oberflächenmessungen
Optische Mikroskope, CNC-Bildmessgeräte, Rauheitsmessgeräte und Wegmesssensoren werden üblicherweise für die Messung der Oberfläche verwendet. Allerdings gibt es Herausforderungen mit der Reproduzierbarkeit, z. B. Schwankungen bei den Ergebnissen der Oberflächenmessung und der Berechnung der Fläche auf der Grundlage von 2D-Daten. Hinzu kommt, dass die Messung aufgrund des hohen Schwierigkeitsgrads viel Zeit in Anspruch nimmt.
Herausforderung bei der Oberflächenmessung mit einem optischen Mikroskop
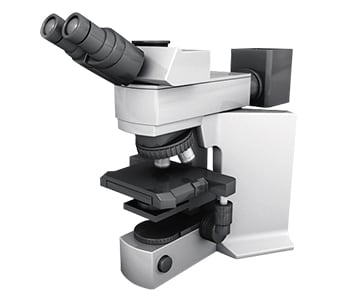
Die Messung mit einem optischen Mikroskop ist für kleine Messobjekte geeignet. Mikroskope, die in den letzten Jahren entwickelt wurden, unterstützen die Quantifizierung der gemessenen Daten und bieten eine einfache Bedienung. Wenn das Messobjekt jedoch groß ist, kann ein Mikroskop nicht zur Messung von Oberfläche, Gesamtfläche und Volumen verwendet werden. Selbst wenn eine Messung möglich ist, erfordert es sehr viel Zeit und Mühe, das Messobjekt während der Messung zu bewegen.
Herausforderung bei der Oberflächenmessung mit einem CNC-Bildmessgerät
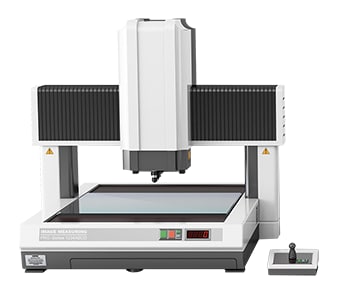
Im Allgemeinen erfasst ein CNC-Bildmessgerät das Messobjekt auf dem Objekttisch mit einer CCD-Kamera und führt eine 3D-Messung durch.
Die Betrachtung anhand von Farbbildern ist möglich, aber bei der Messung der Oberfläche treten folgende Herausforderungen auf:
- Es kann zu Erkennungsfehlern kommen, wenn die Produktoberfläche aufgrund von Produktfehlern wie Graten oder Absplitterungen vorsteht. Wenn die Messpunkte nicht richtig festgelegt sind, kommt es außerdem zu Abweichungen bei der Messung.
- Wenn die Anzahl der Messungen zunimmt, wird das Programm komplex und erfordert sowohl fortgeschrittenes Expertenwissen als auch einen höheren Zeitaufwand für die Konfiguration. Der erforderliche Zeitaufwand für die Prüfung steigt proportional zur Anzahl der Messungen.
Ein weiteres großes Problem ist die Notwendigkeit eines Messraums, welcher auf der Referenztemperatur gehalten werden muss. Außerdem kann eine genaue Messung nicht von allen Mitarbeitern am Arbeitsplatz durchgeführt werden.
Herausforderung bei der Oberflächenmessung mit einem Rauheitsmessgerät oder einem Wegmesssensor
Bei der Messung der Oberflächenrauheit mit einem Rauheitsmessgerät ist die Messung in Höhenrichtung nur auf Punkte oder Linien beschränkt. Daher ist es notwendig, die Anzahl der Messpunkte zu erhöhen, um die Form genau identifizieren zu können. Der Zeitaufwand für eine Messung durch Bewegen eines Messtasters oder Taststifts steigt proportional zur Anzahl der Messpunkte. Zudem muss die Messobjektposition nach der Installation justiert werden. Dennoch sind die gemessenen Werte nur schwer reproduzierbar, da die Messpunkte je nach Anwender variieren können.
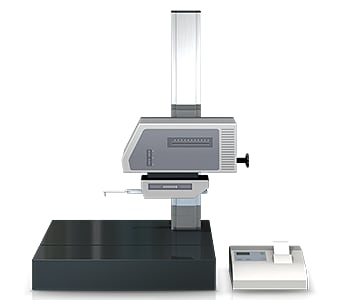
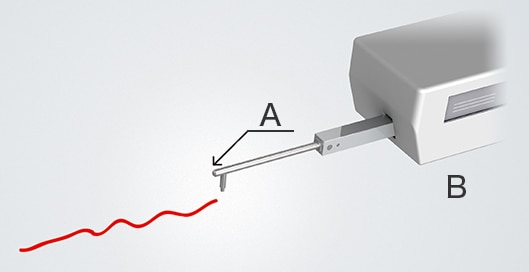
- A
- Taststift
- B
- Detektor
Lösungen für Herausforderungen bei der Oberflächenmessung
Die bisher verwendeten Messgeräte bringen Herausforderungen mit sich, wie z. B. den hohen Zeitaufwand für die Positionierung des Messobjekts und die Tatsache, dass die Messung von dreidimensionalen Messobjekten und Flächen mittels Punkt- oder Linienkontakt erfolgt. Um diese Messprobleme zu lösen, hat KEYENCE das 3D-Profilometer der Modellreihe VR entwickelt.
Die Modellreihe VR erfasst präzise die 3D-Form der gesamten Oberfläche, ohne das Messobjekt zu berühren. Die 3D-Form kann zudem durch einen 3D-Scan des Messobjekts auf dem Objekttisch in nur einer Sekunde mit hoher Präzision gemessen werden. Die Modellreihe VR ist in der Lage, sofortige und quantitative Messungen durchzuführen, ohne fehlerhafte Messergebnisse zu erhalten. In diesem Abschnitt werden einige Vorteile der Modellreihe VR vorgestellt.
Vorteil 1: Messungen großer Flächen von bis zu 300 mm x 150 mm sind möglich.
Legen Sie für die Messung das Messobjekt einfach auf den Objekttisch und starten Sie die Aufnahme per Klick. Eine genaue Positionierung oder sonstige Vorbereitung ist nicht erforderlich. So können auch hochpräzise Messungen von Anwendern, die über keine Kenntnisse oder Erfahrungen im Umgang mit Messgeräten verfügen, durchgeführt werden.
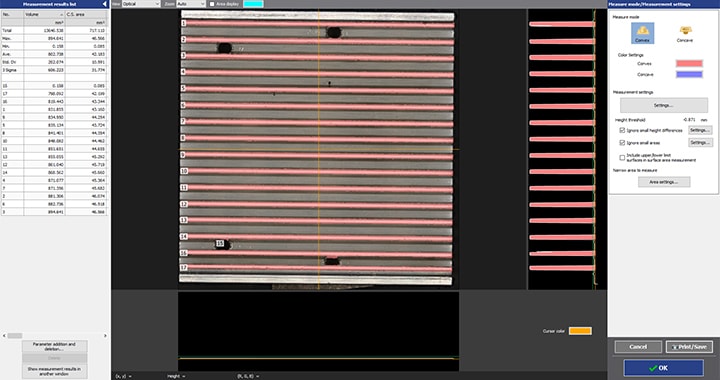
Im Gegensatz zu bisher verwendeten Messgeräten extrahiert die Modellreihe VR die Merkmale des auf dem Objekttisch platzierten Messobjekts und korrigiert automatisch dessen Position. Eine genaue Positionierung, die früher viel Zeit und Mühe erforderte, ist nicht mehr notwendig. Die Modellreihe VR kann auch einen großen Bereich von bis zu 300 mm x 150 mm messen, indem sie mehrere Messbilder zusammenfügt. So können auch unerfahrene Anwender einfach und sofort Messungen durchführen, und es muss kein Fachpersonal dafür beauftragt werden.
Mit der Modellreihe VR können auch Messobjekte mit einer großen Oberfäche, wie z. B. eine Kühlplatte, genau gemessen werden, indem sie einfach auf den Objekttisch gelegt werden und die Messung gestartet wird.
Vorteil 2: Durchführung quantitativer Bewertungen von Oberflächen und Querschnittsflächen.
Bei duktilen Metallbruchflächen ist es möglich, die Oberfläche und die Querschnittsfläche sowie das Verhältnis von Oberfläche zu Querschnittsfläche zu messen.
Mit der Modellreihe VR können Sie anhand der Höhendaten das Volumen und die Fläche des Messobjekts sowie den XY-Durchmesser in der angegebenen Höhe messen. Zählungen können ebenfalls zeitgleich durchgeführt werden.
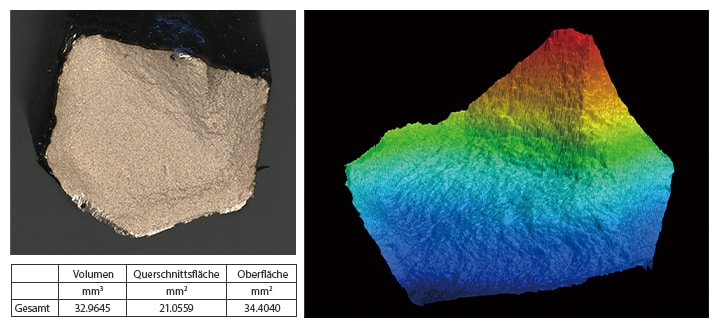
Zusammenfassung: Erhebliche Verbesserung und höhere Effizienz bei komplexen Oberflächenmessungen
Die Modellreihe VR kann 3D-Messobjekte präzise und mit hoher Geschwindigkeit messen, ohne das Messobjekt zu berühren. Das System löst alle Herausforderungen, mit denen handelsübliche Messgeräte konfrontiert sind, indem es die einfache Messung von Oberfläche, Volumen, Querschnittsfläche und Verhältnis von Oberfläche zu Querschnittsfläche ermöglicht.
- Volumen und Oberfläche können gleichzeitig gemessen werden.
- Dies verhindert durch menschliche Faktoren bedingte Abweichungen und ermöglicht so eine zuverlässige quantitative Messung.
- Es sind weder Positionierung noch andere Vorbereitungen erforderlich. Anwender können einfach das Messobjekt auf den Objekttisch platzieren und die Aufnahme per Klick starten. Damit muss für die Messung kein Fachpersonal mehr herangezogen werden.
- 3D-Formen können mit hoher Geschwindigkeit und Genauigkeit gemessen werden. Dadurch ist es möglich, eine große Anzahl von Messobjekten in kurzer Zeit zu messen, was zur Qualitätsverbesserung beiträgt.
Dieses System ermöglicht auch Vergleiche mit früheren 3D-Messdaten und CAD-Daten sowie eine einfache Datenanalyse, wie z. B. die Verteilung innerhalb der Toleranzen. Es kann effektiv für eine Vielzahl von Zwecken eingesetzt werden, einschließlich Produktentwicklung, Trendanalysen in der Produktion und Stichprobenprüfungen.