Messung der Grathöhe an Kunststoff-Formteilen
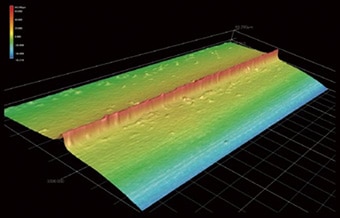
Grate sind typische Formfehler, die beim Spritzgießen und anderen Formen von Kunststoffguss auftreten. Da es schwierig ist, die Spritzgussmaschinen in bestimmten Abständen anzuhalten, ist die Entfernung von Graten, die sich auf einer großen Anzahl von geformten Produkten bilden, mit erheblichen Kosten verbunden. Wenn geformte Produkte mit Graten als fehlerhafte Produkte aussortiert werden, wird die Produktionsquote erheblich reduziert. Das setzt die Gewinnspanne stark unter Druck. Aus diesen Gründen ist es notwendig, Gratformen und -abmessungen präzise zu messen, um die Ursachen so schnell wie möglich zu erkennen und ihr erneutes Auftreten zu verhindern.
Grate, die sich an Endprodukten bilden, haben dreidimensionale Formen, die mit herkömmlichen Messmethoden schwer zu erfassen sind. In diesem Abschnitt werden grundlegende Kenntnisse über Kunststoffgrate und die neueste Messmethode erläutert, die die Herausforderungen bei gängigen Messungen löst.
- Grate an Kunststoff-Formteilen
- Entgratungsmethoden für Kunststoff-Formteile
- Ursachen und Gegenmaßnahmen für Grate an Kunststoff-Formteilen
- Herausforderung bei gängigen Messungen von Grathöhe und -form
- Lösung von Herausforderungen bei der Messung der Grathöhe
- Zusammenfassung
Grate an Kunststoff-Formteilen
Grate sind eine typische Art von Fehlern beim Kunststoffguss. Dieser Formfehler entsteht, wenn geschmolzener Kunststoff in die Form (Patrize und Matrize) eindringt und in der Trennfuge oder in den Lücken um die Auswerferstifte erstarrt.
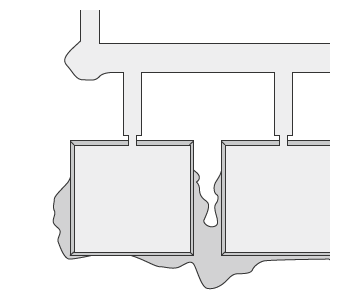
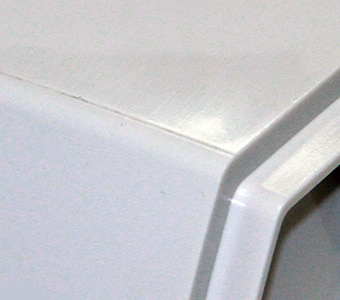
Da Grate unbeabsichtigte Vorsprünge auf dem geformten Produkt sind, können sie die Produktqualität beeinträchtigen. Sie können das Aussehen des Produkts beeinträchtigen oder, wenn sie scharfkantig sind, sogar Verletzungen verursachen. Beim Teilen einer Baugruppe können Grate an Kunststoff-Formteilen die Passgenauigkeit beim Zusammenbau beeinträchtigen. Aus diesen Gründen sollten Grate mit Werkzeugen entfernt werden, wenn das Entgraten möglich und kostengünstig ist.
Entgratungsmethoden für Kunststoff-Formteile
Das Entgraten wird durchgeführt, wenn die Grate, die sich auf Kunststoff-Formteilen bilden, entfernt werden können und die Anzahl der betroffenen Produkte angemessen ist. Das Entgraten kann auch notwendig sein, wenn Formteile aus Produktionsstätten im Ausland Grate aufweisen und die Produkte verwendet werden müssen, um die Lieferfrist einzuhalten.
Manuelles Entgraten
Grate werden manuell entfernt, wenn die Anzahl der zu bearbeitenden Werkstücke gering ist oder wenn sich Grate an Stellen befinden, an denen sie nicht von automatischen Entgratungsmaschinen entfernt werden können.
- Zu den handgeführten Entgratungswerkzeugen gehören Entgratungsfeilen, Fräser, Klingen und Schleifscheiben.
- Thermoplastische Grate werden entfernt, indem sie mit der Hitze eines Lötkolbens oder eines anderen Werkzeugs weggeschmolzen werden (diese Methode kann verwendet werden, wenn die Grate dünn sind und das geformte Produkt dick ist).
- Grate werden entfernt, nachdem sie durch Einfrieren spröde gemacht wurden (diese Methode kann verwendet werden, wenn die Grate dünn sind und das geformte Produkt dick ist).
Andere Methoden wie Schleifwerkzeuge und Chemikalien können unter Berücksichtigung des Formmaterials, der Eigenschaften des geformten Produkts und der Grate, der Verarbeitbarkeit und anderer Faktoren eingesetzt werden.
Entgraten mit Maschinen
Wenn Produkte in komplexe Formen gegossen werden, kann es sein, dass das Auftreten von Graten an bestimmten Stellen aufgrund der Struktur der Form bis zu einem gewissen Grad toleriert werden muss. Wenn die Formen der geformten Produkte hingegen einfach sind, kann das Entgraten mit einer automatischen Entgratungsmaschine oder einer anderen Maschine als ein Schritt in den Kunststoff-Formungsprozess aufgenommen werden.
- Strahltechnik: Grate werden entfernt, indem das Strahlmittel (z. B. Sand oder kugeliges Strahlmittel) in der Maschine auf die geformten Produkte gestrahlt wird. Die entfernten Grate werden automatisch von einem eingebauten Staubfänger aufgefangen.
- Hochdruckwasserstrahlmaschine: Die Grate werden entfernt, indem Wasser mit Hochdruck auf die geformten Produkte gestrahlt wird. Dieser Prozess dient auch zur Reinigung der geformten Produkte.
- Ultraschallschneider: Eine mit Ultraschallfrequenz vibrierende Klinge berührt und entfernt den Grat. Da die mikrovibrierende Klinge mit thermoplastischem Kunststoff in Berührung kommt, der durch die Hitze der Kunststoffmoleküle erweicht wurde, ist es möglich, Grate zu entfernen, ohne die geformten Produkte stark zu belasten.
Neben den oben genannten gibt es noch verschiedene andere Arten von automatischen Entgratungsmaschinen. Der Maschinentyp wird nach den Eigenschaften des thermoplastischen Kunststoffs, Duroplasts oder eines anderen Kunststoffs ausgewählt, der für die geformten Produkte verwendet wird, sowie nach Faktoren wie Größe, Form und Haltbarkeit der geformten Produkte.
Identifizierung der Formen und Abmessungen für eine angemessene Entgratung
Um die Entgratungsmethode auszuwählen und sich für eine geeignete Entgratungsmaschine zu entscheiden, ist es wichtig, so viele Informationen wie möglich über die Grate zu erhalten. Grate haben dreidimensionale Formen, selbst wenn sie dünn sind. Das macht es in vielen Fällen schwierig, ihre Höhen und Formen mit herkömmlichen Messsystemen präzise zu erfassen. Diese Herausforderung bei der Messung von Graten und eine Lösung dafür werden später erläutert.
Ursachen und Gegenmaßnahmen für Grate an Kunststoff-Formteilen
Wenn eine größere Anzahl fehlerhafter Kunststoff-Formteile durch unerwartete Grate entsteht, erfordert dies einen hohen Zeitaufwand und hohe Kosten für das Entgraten. Daher wird auf jeden Fall empfohlen, das Entstehen von Graten von vornherein zu verhindern und die Prozesse zu verbessern, um ein erneutes Auftreten von Graten zu vermeiden.
In diesem Abschnitt werden Beispiele typischer Ursachen für die Entstehung von Graten beim Spritzgießen und Gegenmaßnahmen zu deren Vermeidung vorgestellt.
Beispiele für Ursachen, die zu Gratbildung beim Spritzgießen führen
- Niedriger Formschließdruck im Vergleich zum Einspritzdruck des geschmolzenen Kunststoffs
- Geringe Präzision der Trennfuge zwischen den Formen (Patrize und Matrize)
- Übermäßig hohe Fließeigenschaften des geschmolzenen Kunststoffs (möglicherweise verursacht durch eine zu hohe Temperatur der Form oder des geschmolzenen Kunststoffs)
- Lücken zwischen den Formen, die durch Belastung oder andere Faktoren entstanden sind
- Ungleichgewicht in der Menge des eingespritzten geschmolzenen Kunststoffs, der Schließkraft der Form und des Einspritzdrucks
- Ungleichgewicht zwischen der projizierten Fläche im Inneren der Form und der Schließkraft der Form (Kraft, die den Druck aufrechterhält)
- Verspannte oder gekippte Formplatte in der Spritzgießmaschine
Grate können aber auch durch viele andere Ursachen entstehen.
Beispiele für Gegenmaßnahmen zur Vermeidung von Gratbildung beim Spritzgießen
- Erhöhen Sie den Schließdruck der Form oder verringern Sie den Einspritzdruck des Kunststoffs.
- Passen Sie die Formen so an, dass sie an der Trennfuge fest sitzen.
- Verbessern Sie die Formen durch Einsätze, Schweißen oder andere Mittel, um die Lücken zwischen der Patrize und der Matrize zu beseitigen.
- Wenden Sie einen Nachdruck an, der für den projizierten Bereich der Form geeignet ist, und passen Sie ihn an, während Sie das Gleichgewicht mit der Formschließkraft überprüfen.
- Die Formtemperatur kann höher sein als die mit dem Regler eingestellte Temperatur. Passen Sie die Temperatureinstellung an, während Sie die tatsächliche Formtemperatur messen.
- Wenn das Fließen des Kunststoffs am Formanguss schlecht ist, erhöht eine übermäßige Erhöhung der Temperatur und der Fließeigenschaften des Kunststoffs die Wahrscheinlichkeit, dass der Kunststoff aus der Trennfuge herausfließt. Überprüfen und verbessern Sie daher den Formanguss auf der Grundlage einer geeigneten Kunststofftemperatur.
Da die Präzision der Form und der Formmaschine, der Formschließdruck, die Temperatur und der Druck der Form und des Kunststoffs sowie andere Faktoren alle miteinander zusammenhängen, liegt der Schlüssel zu wirksamen Gegenmaßnahmen in der Überprüfung und Korrektur dieser Faktoren aus einer umfassenden Perspektive.
Erwägen von Gegenmaßnahmen auf der Grundlage der Gratformen bei fehlerhaften Produkten
Die Grate, die an einem geformten Produkt auftreten, können Hinweise auf die Ursache liefern. Nicht nur die Grathöhe und -dicke können problematische Formstellen der Form anzeigen, sondern auch die Größe der Lücke der Trennfuge und die Fließeigenschaft des geschmolzenen Kunststoffs, während der Kegelwinkel des Grats eine Belastung der Form oder eine örtliche Abnahme der Formgenauigkeit anzeigen kann.
Die genaue Identifizierung der Stellen, Formen und Messungen von Graten an fehlerhaften Produkten ermöglicht die Gewinnung wichtiger Informationen für die Durchführung von Verbesserungen und Maßnahmen zur Verhinderung eines erneuten Auftretens.
Herausforderung bei gängigen Messungen von Grathöhe und -form
Wie im vorherigen Abschnitt erwähnt, kann eine präzise Messung der Formen und Abmessungen von Graten an Kunststoff-Formteilen dazu beitragen, die Stellen und Ursachen von Graten zu identifizieren, ihr erneutes Auftreten zu verhindern und die Entgratungsbedingungen festzulegen. Die Höhenmessung von dreidimensionalen Graten mit gängigen Profilmesssystemen oder Mikroskopen ist mit folgenden Herausforderungen verbunden:
Herausforderungen bei der Messung von Grathöhe und -form mit einem Profilmesssystem
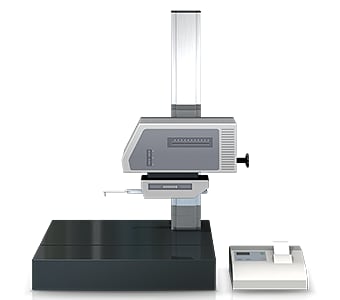
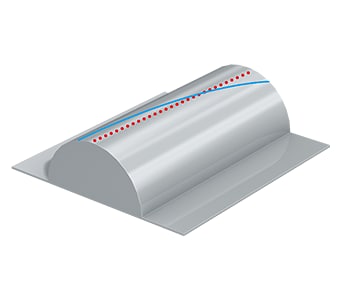
Bei der Messung der Grathöhe mit einem Profilmesssystem oder Konturograph ergeben sich die folgenden Herausforderungen:
- Die Messung erfordert viel Zeit, einschließlich der Zeit für die Befestigung des Messobjekts auf einer Vorrichtung und dessen Nivellierung. Es sind zudem Kenntnisse und Fähigkeiten im Umgang mit Profilmesssystemen erforderlich, um ein Messobjekt genau zu nivellieren.
- Bei der Messung von Graten in vertieften Stellen ist es schwierig, die gewünschte Messposition mit dem Taststift nachzuzeichnen. Schon eine leichte Verschiebung des Taststifts führt zu Abweichungen bei den Messwerten.
- Es ist schwierig, das Messobjekt so zu platzieren, dass die durch den höchsten Punkt eines zylindrischen Messobjekts verläuft.
- Der Taststift bewegt sich in einem Bogen auf und ab, der auf dem Drehpunkt des Tastarmes zentriert ist, und die Tastspitze bewegt sich auch in Richtung der X-Achse. Dies führt zu Fehlern in den Daten auf der X-Achse.
Herausforderung bei der Messung von Grathöhe und -form mit einem Mikroskop
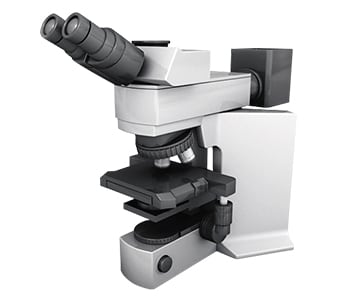
Im Gegensatz zu Profilmesssystemen können Mikroskope Oberflächeninformationen erfassen. Rillenbreiten können je nach Ausmaß der Objekttischbewegung gemessen werden und die Tiefe kann anhand der Fokuseinstellung gemessen werden. Bei der Messung mit einem Mikroskop treten jedoch folgende Herausforderungen auf:
- Bei der Betrachtung von Graten auf Kunststoff-Formteilen mit hoher Vergrößerung ist es aufgrund des kleinen Sichtfelds schwierig, die gesamte Gratform zu erkennen.
- Da die Messung vom menschlichen Auge abhängt, können die Messergebnisse je nach Anwender variieren.
- Da Mikroskope grundsätzlich nicht als Messsysteme gedacht sind, sind sie nicht immer in der Lage, die Messergebnisse zu quantifizieren oder zuverlässige Messwerte zu liefern.
Lösung von Herausforderungen bei der Messung der Grathöhe
Kunststoff-Formteile und die Grate, die sich an diesen Teilen bilden, haben dreidimensionale Formen. Das macht es schwierig, sie mit handelsüblichen Messmethoden präzise zu messen. Ein großes Problem ist auch die Tatsache, dass die Messung nicht nur Geschicklichkeit, sondern auch viel Zeit und Arbeit erfordert.
Um diese Herausforderung bei der Messung der Grathöhe zu lösen, hat KEYENCE das 3D-Profilometer der Modellreihe VR entwickelt.
Die Modellreihe VR erfasst präzise die 3D-Form der gesamten Oberfläche, ohne das Messobjekt zu berühren. Ein 3D-Scan des Messobjekts kann in nur einer Sekunde abgeschlossen werden, wodurch eine schnelle Messung der 3D-Form möglich ist. Das System ist in der Lage, sofortige und quantitative Messungen durchzuführen. In diesem Abschnitt werden einige Vorteile der Modellreihe VR vorgestellt.
Vorteil 1: Die 3D-Form der gesamten Messobjektoberfläche kann mit einer einzigen Messung präzise und vollständig in nur einer Sekunde erfasst werden
Die Modellreihe VR erfasst mit einer Aufnahme mehrere hunderttausend Messpunkte. Verschiedene Profillinien wie z. B. lotrechte, parallele und senkrechte Linien können ebenfalls durch einfache und intuitive Vorgänge an den gewünschten Stellen gesetzt werden. Da auch eine präzise Profilmessung möglich ist, können Anwender sofort detaillierte Daten erfassen, die für die Identifizierung der Ursachen von Graten unerlässlich sind.
Sogar nach der Messung kann die Profilmessung auch an älteren Daten jederzeit durchgeführt werden, ohne dass das Messobjekt erneut gescannt werden muss.
Die maximalen und minimalen Oberflächenunregelmäßigkeiten (Höhe, Tiefe) können farblich dargestellt werden, um fehlerhafte Bereiche auf dem gesamten Messobjekt deutlich zu visualisieren.
Darüber hinaus können Messdaten von mehreren Messobjekten nebeneinander verglichen werden, und die gewünschten Bedingungen können auf mehrere Datensätze gleichzeitig angewendet werden. Dies führt zu einer erheblichen Reduzierung des Zeitaufwands und einer verbesserten Arbeitseffizienz.
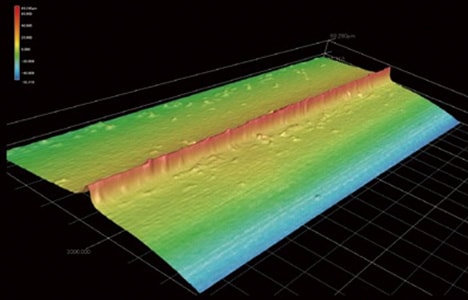
Vorteil 2: Graterkennung und Messung über einen großen Bereich
Bei Gratmessungen ist es oft notwendig, die maximale Grathöhe zu ermitteln. Da die Lage des höchsten Grats bei jedem einzelnen Messobjekt unterschiedlich ist, müssen Daten für das gesamte Messobjekt erfasst werden. Die Modellreihe VR kann eine große Fläche messen und ermöglicht so eine schnelle und präzise Messung der Gratspitzen durch eine einfache Bedienung.
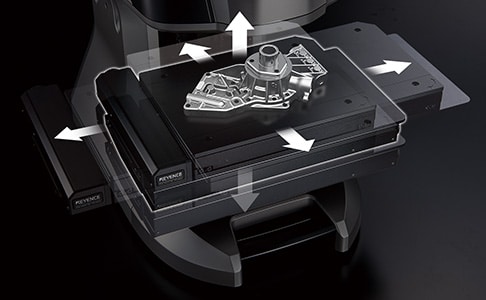
Die Messung von 3D-Formen kann ganz einfach durchgeführt werden, indem Sie das Messobjekt auf den Objekttisch legen und die Aufnahme starten. Da eine automatische Positionskorrektur anhand von Messobjektdaten möglich ist, ist eine genaue Nivellierung oder Positionierung nicht erforderlich. Diese Modellreihe umfasst auch die neue „Smart Measurement“-Funktion, die den Messbereich automatisch konfiguriert und den Objekttisch entsprechend der Größe des Messobjekts bewegt. Damit entfällt die Arbeit, die bislang für die Einstellung der Messlänge und des Z-Bereichs erforderlich war.
Die große Auswahl an Hilfswerkzeugen ermöglicht eine einfache und intuitive Konfiguration der gewünschten Messungen.
Zusätzlich zur einfachen Konfiguration ermöglichen die Hilfswerkzeuge eine einfache Bedienung des Systems, sodass selbst ungeübte Anwender, die mit Messungen nicht vertraut sind, Formen in nur einer Sekunde präzise messen können. Zusätzlich zu Zwecken wie Forschung, Entwicklung und Formversuchen ist es damit möglich, die Anzahl der Proben einfach zu erhöhen oder Trendanalysen für Messungen und Prüfungen während der Massenproduktion durchzuführen.
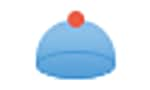
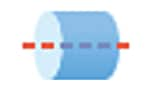
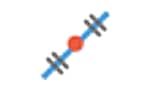
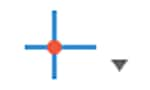
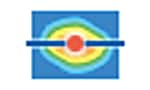
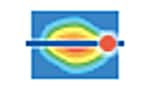
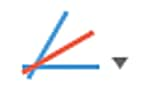
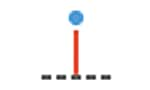
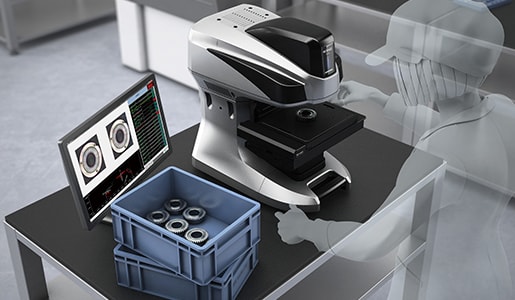
Zusammenfassung
Die Modellreihe VR kann schnell und einfach Oberflächendaten erfassen, ohne das Messobjekt zu berühren. Neben der 3D-Messung des gesamten Kunststoff-Formteils kann die Modellreihe VR auch schwierige Messungen wie feine Grathöhen und Formen von Oberflächenunregelmäßigkeiten in nur einer Sekunde durchführen.
Die Modellreihe VR löst viele Herausforderungen, die bei gängigen Messgeräten auftreten können.
- Die maximale Höhe und die Formen der Grate über einen großen Bereich können in einer Farbkarte visualisiert werden.
- Sobald ein Scan abgeschlossen ist, können Sie jederzeit eine Profilmessung einer beliebigen Stelle und einen Vergleich mehrerer Datensätze durchführen.
- Es sind weder Positionierung noch andere Vorbereitungen erforderlich. Anwender können einfach das Messobjekt auf den Objekttisch platzieren und die Aufnahme per Klick starten. Damit muss für die Messung kein Fachpersonal mehr herangezogen werden.
- Da 3D-Formen mit hoher Geschwindigkeit und Präzision gemessen werden können, ist die Messung einer großen Anzahl von Proben in kurzer Zeit möglich. Dies ist nützlich für Qualitätsverbesserungen.
- Dies verhindert durch menschliche Faktoren bedingte Abweichungen und ermöglicht so eine zuverlässige quantitative Messung.
Dieses System ermöglicht Vergleiche mit CAD-Daten und eine einfache Datenanalyse, wie z. B. die Verteilung innerhalb der Toleranzen. Neben Forschung, Entwicklung und Formversuchen kann es in einer Vielzahl von Situationen an Arbeitsplätzen in der Kunststoffverarbeitung effektiv eingesetzt werden, z. B. bei Stichprobenprüfungen nach Beginn der Massenproduktion und bei der Ursachenanalyse, wenn Fehler auftreten.