Messung von Chip-Bauteilen
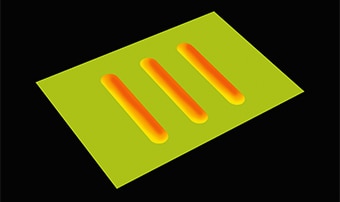
Neue Technologien zur Leiterplattenbestückung werden immer komplexer, um dem Bedarf an kleineren, leichteren und dünneren Anschlussklemmen, wie z. B. für Smartphones und Heimelektronik, sowie an kleineren elektronischen Komponenten, wie z. B. Chip-Widerständen und Keramikkondensatoren, gerecht zu werden. In diesem Abschnitt werden Herausforderungen vorgestellt, die bei bestückten Komponenten auftreten können. Zudem wird erläutert, wie 3D-Messsysteme eingesetzt werden können, um diese Herausforderungen zu beurteilen, zu analysieren und zu vermeiden.
- Methode zur Bestückung von Chip-Komponenten
- Was ist Aufschmelzlöten?
- Regelung der Temperatur im Aufschmelzofen
- Herausforderungen bei der Oberflächenbestückung
- Beispiel einer Wölbungsmessung an einer Leiterplatte
- Beispiel einer Koplanaritätsmessung an den Anschlüssen eines Aluminiumkondensators
- Beispiel einer Dickenmessung von Lötpaste
- Beispiele einer Messung der Schichtdicke bei Widerständen
- Beispiel einer Tiefenmessung von Rissen in Schichten
- Breitenmessung eines Dielektrikums
Methode zur Bestückung von Chip-Komponenten
Neben der Miniaturisierung von elektronischen Komponenten und der höheren Dichte der Leiterplattenbestückung ist das Aufschmelzlöten zum Standard geworden.
Lötverfahren | Eigenschaften | |
---|---|---|
Vorteile | Nachteile | |
Lötkolben |
Geringe thermische Belastung |
Hohe Temperaturschwankung |
Heißluft |
Geringe thermische Belastung |
Hohe Temperaturschwankung |
Laser |
|
Nicht für die Massenproduktion geeignet (lange Verarbeitungszeit) |
Impulswärme |
|
Nicht für die Massenproduktion geeignet (lange Verarbeitungszeit) |
Aufschmelzlöten (Infrarottyp) |
|
|
Aufschmelzlöten (Heißlufttyp) |
|
|
Flow-Löten |
|
|
Was ist Aufschmelzlöten?
Lötpaste, eine Mischung aus Flussmittel und kleinen Lotpartikeln, wird auf eine Metallplatte mit darin gestanzten Löchern aufgetragen und mit einem Spachtel zu einer dünnen Schicht aufgetragen. Die Komponenten werden dann auf die Leiterplatte montiert, erwärmt und gelötet.


Wenn es sich um wenige Komponenten handelt, kann die Bestückung auch per Hand durchgeführt werden.

Die Temperatur wird in fünf Schritten geregelt (siehe folgender Abschnitt).
Regelung der Temperatur im Aufschmelzofen
Normalerweise wird die Hitze in zwei Schritten angewandt. Im ersten Schritt wird die Leiterplatte auf eine gleichmäßige Temperatur gebracht, die über einen bestimmten Zeitraum gehalten wird. Im zweiten Schritt wird die Lötpaste geschmolzen. Die erforderlichen Temperaturen und Zeiten hängen vom jeweiligen Aufschmelzofen und von den jeweiligen Komponenten ab.

Herausforderungen bei der Oberflächenbestückung



Beispiel einer Wölbungsmessung an einer Leiterplatte
Wölbungen an Leiterplatten werden durch Temperaturschwankungen verursacht, die bei der Stromzufuhr auftreten, sowie durch Veränderungen der Umgebung. Die Analyse wird durchgeführt, um festzustellen, ob aufgrund dieser Temperaturänderungen Defekte aufgetreten sind.



Beispiel einer Koplanaritätsmessung an den Anschlüssen eines Aluminiumkondensators
Mangelhafte Ebenheit von Kondensatorklemmen, die Bestückungsfehler verursachen und sich auf die Bestückungsgenauigkeit der Leiterplatte auswirken kann, ist messbar.

Beispiel einer Dickenmessung von Lötpaste
Die Schichtdicke, der auf einer Leiterplatte aufgetragenen Lötpaste, kann gemessen werden.

Beispiele einer Messung der Schichtdicke bei Widerständen
Die Schichtdicke und das Volumen eines Widerstands im flüssigen Zustand kann vor dem Sintern gemessen werden, nachdem die Schicht gedruckt wurde.
Dadurch können die Bedingungen für den Sinterprozess effizient eingestellt werden.

Chip-Widerstand-Aufbau
Chip-Widerstände sind kleine quadratische Festwiderstände, die aus Widerstandselementen bestehen, die auf der Oberfläche einer isolierenden Basis, wie beispielweise Keramik, gebildet werden und Elektroden an beiden Enden aufweisen. Sie eignen sich vor allem für die Oberflächenbestückung.
Typischer Aufbau eines quadratischen Chip-Widerstands
- ・ Kein Zuleitungsdraht an den Anschlusselektroden
- ・ Löten oder Bonden ist möglich
* MELF-Widerstände mit zylindrischer Form sind auch verfügbar, werden aber nicht häufig verwendet.

- A
- Schutzschicht
- B
- Außenverkleidung
- C
- Anschlusselektrode
- D
- Keramik
- E
- Widerstandsschicht
- F
- Interne Elektrode
- G
- Nickelbeschichtung
- Keramik (Basis)
- Die Basis besteht aus einer Keramikplatte, um das Sintern oder Laser-Trimmen des Widerstandselements zu ermöglichen.
- Widerstandselement
- Es gibt Dick- und Dünnschichttypen. Das Widerstandselement hat einen Aufbau von mindestens drei Schichten.
- Elektrode
- Das Widerstandselement ist über interne Elektroden mit den Anschlusselektroden verbunden.
- Schutzschicht
- Die Oberfläche des Widerstandselements ist mit Harz oder Glas beschichtet, um ein direktes Anhaften von Feuchtigkeit oder Staub zu verhindern.
Beispiel einer Tiefenmessung von Rissen in Schichten
Die Dicke und Ausdehnung von Schichten kann gemessen werden, um sicherzustellen, dass Chip-Widerstände innerhalb der vorgegebenen Spezifikation bleiben.
Die Breite und Tiefe von Rissen, kann ebenfalls gemessen werden.

Laser-Trimmen
Die Schichten eines Chip-Widerstands werden im Siebdruckverfahren gebildet. Da auf einer Keramikbasis mehrere hundert Widerstandselemente gebildet werden, führen schon kleinste Abweichungen der Druckbedingungen direkt zu Schwankungen des Widerstands.
Wenn der Widerstand zwischen den Chip-Widerständen variiert, erfüllen die elektrischen Eigenschaften nicht die Anforderungen. Deshalb ist das Laser-Trimmen zur Einstellung des Widerstands notwendig. Beim Laser-Trimmen werden Widerstandselemente nacheinander gemessen und beschnitten, um den vorgegebenen Widerstand zu gewährleisten und Schwankungen zu minimieren.
- 1. Widerstandselemente werden gedruckt, indem man zunächst einen etwas niedrigeren Widerstand als den Sollwiderstand erzeugt.
- 2. Das Trimmen eines Widerstandselements macht seinen Strompfad schmaler, was den Widerstand erhöht.
- 3. Das Trimmen wird beendet, wenn der Sollwiderstand erreicht ist, um Schwankungen zwischen Chips zu minimieren.

- A
- Elektrischer Stromfluss
- B
- Laser-Trimmen
- C
- Eine kurze Trimmlänge bewirkt eine kleine Änderung des Widerstands.
- D
- Eine lange Trimmlänge bewirkt eine große Änderung des Widerstands.
* Je länger das Element getrimmt wird, desto schmaler wird der Strompfad im Widerstandselement und desto höher steigt der Widerstand.
Die endgültige Trimmlänge und -form wird basierend auf der Änderung des Widerstands beim Trimmen bestimmt.
Wenn die Änderungen des Widerstands aufgrund der Schnittlänge zwischen geradem Schneiden und L-förmigem Schneiden verglichen werden, kann das L-förmige Schneiden eine höhere Präzision beim Endschnitt bieten und den Einfluss von Mikrorissen am Ende reduzieren.


Breitenmessung eines Dielektrikums
Die Rasterbreite und -dicke eines Dielektrikums im flüssigen Zustand kann gemessen werden.

Struktur eines Keramikvielschicht-Chipkondensators
Die Grundstruktur eines Kondensators besteht aus einem Dielektrikum zwischen zwei Elektrodenplatten.
- 1. Dielektrisches Material wie Bariumtitanat (BaTiO3), ein keramisches Dielektrikum, wird auf eine Trägerfolie aufgebracht.
- 2. Das Material wird getrocknet, um eine dünne Folie zu erzeugen.
- 3. Die Paste aus Elektrodenmaterial, die Metalle wie Palladium, Silber oder Nickel enthält, wird auf die Folie gedruckt.
- 4. Die Folien werden in 10 bis 1000 Lagen gestapelt, gepresst und zu Chips geschnitten.
- 5. Die letzten Schritte bei der Herstellung von Keramikvielschicht-Chipkondensatoren sind das Sintern und das Versilbern der externen Anschlussklemmen.
Beim Sintern von Keramik schrumpfen die Chips um etwa 10%, was bei der Dimensionierung berücksichtigt werden muss.

- A
- Externe Elektrode
- B
- Interne Elektrode
- C
- Keramisches Dielektrikum
Proportionale Beziehung zwischen elektrostatischer Kapazität und Elektrodenplattenfläche
Da die Parallelschaltung mehrerer Kondensatoren gleichbedeutend ist mit einer Vergrößerung der Fläche der Elektrode, kann die elektrostatische Kapazität durch Erhöhung der Anzahl der Kondensatoren erhöht werden.
Die Verwendung mehrerer Kondensatoren nimmt viel Platz auf der Leiterplatte in Anspruch, weshalb diese Methode nicht geeignet ist, wenn Platz gespart werden soll.
Um dies zu vermeiden, erreichen Keramikvielschicht-Chipkondensatoren sowohl die Miniaturisierung als auch eine hohe Kapazität, indem mehrschichtige Strukturen aus keramischen Dielektrika und Innenelektroden im Wechsel gestapelt werden.