Messung und Prüfung von Farbfehlern, Schichtdicke und Pigmentdispersion
Die Anforderungen an Farben und Lacke haben sich im Laufe der Zeit gewandelt, von Ästhetik und Haltbarkeit bis hin zu ökologischem und ökonomischem Design.
Farben und Lacke gibt es in einer Vielzahl von Varianten für unterschiedliche Bereiche wie das Bauwesen, die Automobilindustrie und andere industrielle Anwendungen. Zum Beispiel erfordert die Lackierung von Automobilkarosserien ein Höchstmaß an Qualität hinsichtlich verschiedener Eigenschaften wie Ästhetik, Witterungsbeständigkeit und Ausbleichschutz.
In diesem Abschnitt werden anhand von Beispielen und anschaulichen Bildern die Grundkenntnisse über Lacke, Farben und Beschichtungen sowie die Betrachtung und Messung mit dem Digitalmikroskop der Modellreihe VHX sowie entsprechende Lösungsansätze vorgestellt.
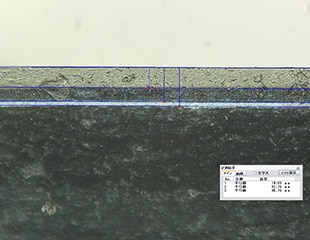
- Materialien lackieren
- Lackierungstechniken
- Beschichtungsfehler und Lösungen
- Prüfung der Schichtdicke
- Aktuelle Beispiele für die Messung und Betrachtung von Lackierungen und Beschichtungen
- Allgemeine Praktiken für die Messung und Analyse von Lackierungen und Beschichtungen
Materialien lackieren
Lack ist ein chemisches Produkt, das aus vielen verschiedenen Bestandteilen zusammengesetzt ist. Die Eigenschaften des Lacks werden durch das Bindemittel, die filmbildende Komponente des Lacks, bestimmt, während das Pigment Rost verhindert und dem Lack seine Farbe verleiht.
Das Bindemittel verleiht dem Lack seine filmbildende Eigenschaft (Trocknungsverhalten), physikalische Funktionen (Elastizität und Filmhaftung) und chemische Funktionen (Haltbarkeit und chemische Beständigkeit des Films). Die Hauptsubstanz des Bindemittels ist Kunstharz. Lack mit einem durch Harz wasserlöslich gemachten oder in Wasser dispergierten Bindemittel wird als Lack auf Wasserbasis bezeichnet. Als Pulverlack wird Lack bezeichnet, der in Pulverform vorliegt und durch Druckluft fluidisiert wird.
Pigmente sind feine, lichtechte Farbpartikel, die sich nicht in Wasser oder anderen Lösungsmitteln auflösen. Pigmente können in drei Klassen eingeteilt werden: Farbpigmente, rosthemmende Pigmente und Streckpigmente. Farbpigmente verleihen dem Lack seine Farbe. Einige Beispiele sind Titanweiß, Rußschwarz, Ockergelb, Karbonblau, Cyaningrün und Chinacridon-Rot. Zu den rosthemmenden Pigmenten gehören Aluminiumphosphat, Zinkmolybdat und Zinkstaub. Streckpigmente bestimmen die Filmeigenschaften. Beispiele sind Glanzpigmente, die den Glanz der getrockneten Farbe beeinflussen, Funktionspigmente wie Aluminiumpulver und fluoreszierende oder phosphoreszierende Pigmente sowie Spezialpigmente wie Infrarotreflexionsmittel und Ferrit-Funkwellenabsorber.
Lackierungstechniken
Die Lackierung bildet einen Farbfilm. Die durch die Lackierung entstehende Schichtdicke beträgt in der Regel zwischen einigen wenigen und mehreren hundert Mikrometern. Da der Anstrich eine gewisse Funktion haben kann, stellt die Lackierung einen Prozess dar, der die Kosteneffizienz erheblich beeinflussen kann.
Die Lackierung ist ein dreistufiger Prozess: Vorbehandlung, Auftrag und Trocknung. Bei Mehrschichtlackierungen wird dieser Vorgang wiederholt.*
Als Vorbehandlung wird die Oberfläche des Materials gereinigt. Grob unterschieden werden Nass- und Trockenverfahren: Typischerweise werden Nassbeschichten bzw. Sandstrahlen eingesetzt.
Lack kann in flüssiger oder gasförmiger Form durch Sprühen aufgetragen werden. Zum Auftragen von Flüssiglack eignen sich Pinsel, Vorhangfließbeschichter, bei dem der Lack unter einem Wasserstrahl aus oben liegenden Schlitzen auf das Werkstück aufgetragen wird, oder Walzenbeschichtungsanlagen, die den Lack mit einer Gummiauftragsrolle auf das Werkstück übertragen. Die Sprühbeschichtung erfolgt mit einem Druckluftsprühsystem, durch elektrostatische Sprühsysteme, bei dem eine negative Ladung auf den Lack aufgebracht wird, während das Werkstück positiv aufgeladen wird, oder durch Pulverbeschichtungsanlagen, bei denen der Pulverlack elektrostatisch aufgeladen wird.
Bei der Mittel- und Deckbeschichtung kann die Vorbehandlung entfallen.
Beschichtungsfehler und Lösungen
Lackierungen können Mängel aufweisen, wenn es Probleme bei der Oberflächenvorbehandlung, den Witterungsverhältnissen zum Zeitpunkt der Lackierung, dem Lack selbst oder der Auftragsmethode gibt. Die Untersuchung des entstandenen Fehlers zur Ermittlung der Ursache ist unerlässlich für die Auswahl eines geeigneten Lacks, die Verbesserung der Auftragsmethode und andere Vorsichtsmaßnahmen, um das erneute Auftreten des gleichen Fehlers zu verhindern.
Im Folgenden werden einige typische Lackierfehler genannt und die möglichen Ursachen und deren Vermeidung erläutert.
Kraterbildung
Kraterförmige Löcher im Lack werden typischerweise durch das Anhaften von Fremdpartikeln im erstarrenden Lack verursacht. Fremdpartikel können durch Menschen oder Maschinen verursacht werden, die während des Abdeck- oder Poliervorgangs Schmutz oder Schwebeteilchen aufwirbeln, die am Werkstück haften. Kunststoffprodukte können sich elektrostatisch aufladen, wenn sie nach dem Umformen aus ihren Formen entnommen werden. Luftgetragene Fremdpartikel werden dann von diesen Formen angezogen und bleiben am Produkt haften.
Die Reinigung rund um die Lackieranlagen und das Anbringen von Abdeckungen an Förderbändern sind wirksame Maßnahmen, um das Anhaften von luftgetragenen Fremdpartikeln zu verhindern. Ionisatoren können zur Beseitigung elektrostatischer Fremdpartikelanhaftungen nützlich sein. Wenn sich der Lack verfestigt, muss das Verdünnungsmittel gewechselt und/oder der Rührvorgang korrigiert werden. Das Filtern des Lacks ist eine weitere Möglichkeit, das Erstarren effektiv zu verhindern.
- Erscheinungsbild:
- Auf der lackierten Oberfläche befinden sich kraterförmige Löcher.
- Mögliche Ursachen:
- Fremdkörper haben sich auf der lackierten Oberfläche abgelagert.
Es befinden sich verfestigte Lackstücke oder Fremdkörper im Lack.
Luftgetragene Fremdpartikel haben sich auf der lackierten Oberfläche festgesetzt, bevor diese getrocknet ist.
- Fehlervermeidung:
- Sorgfältige Reinigung der Oberfläche bei der Vorbehandlung.
Lack filtern, um Fremdkörper zu entfernen.
Staubschutzmaßnahmen durchführen.
Rissbildung
Die Rissbildung hat eine Reihe verschiedener möglicher Ursachen, die vom Lackiermaterial und der Art der Lackierung des Werkstücks abhängen.
So können z. B. Risse in einer Mehrschichtlackierung auftreten, wenn die Haftung zwischen Grund- und Decklackschicht schlecht ist oder die Grundierung nicht ausreichend getrocknet wurde. In solchen Fällen muss eventuell der Lack gewechselt oder die Trocknungszeit für die Grundierung verlängert werden.
Da Rissbildung aus einer Reihe von Gründen, einschließlich der Alterung, auftreten kann, ist es wichtig, bei der Ermittlung der Ursache den Zustand der Lackschicht sorgfältig zu untersuchen.
- Erscheinungsbild:
- Auf der Lackfläche sind Risse vorhanden.
- Mögliche Ursachen:
- Die Oberfläche war rissig.
Die Beschichtung war zu dick.
Falsches Verhältnis Lack/Härter (bei binären Lacken).
Die Auswahl des Verdünners war ungeeignet (falls Verdünner verwendet wurde).
- Fehlervermeidung:
- Risse auf der Oberfläche des Werkstücks während der Vorbehandlung beseitigen.
Zu dicker Auftrag ist zu vermeiden, da dies zur Antrocknung führen kann.*
Den Lack vor Gebrauch ausreichend aufrühren.
Die angegebene Menge an Härter verwenden.
Antrocknung: Ein Zustand, bei dem nur die Oberfläche der Beschichtung getrocknet ist und der Lackfilm noch nicht ausgehärtet ist.
Lackablösung
Eine Lackablösung tritt typischerweise dann auf, wenn die Oberflächenbehandlung unzureichend war oder wenn sich der Lack nicht an das Trägermaterial anpasst bzw. die Haftung von der Lackschicht zum Untergrund nicht ausreichend ist.
Die Oberfläche des Werkstücks mit einer Tellerschleifmaschine von Rost und alter Farbe befreien und vor dem Auftragen der Farbe alle Fremdkörper und Fett von der Oberfläche abwischen. Die Lackablösung, die durch eine mangelnde Haftung zwischen dem Lack und dem Trägermaterial oder der Grundierung und der Decklackschicht verursacht wird, wird als Zwischenschichtablösung bezeichnet und erfordert eine Änderung der Lackkombinationen und/oder eine andere Auftragsmethode.
Die Vorbehandlung ist sehr wichtig für eine einwandfreie Lackierung.
- Erscheinungsbild:
- Die Beschichtung verliert an Haftung und blättert ab.
- Mögliche Ursachen:
- Die Vorbehandlung der Oberfläche, wie z. B. das Entrosten, war nicht ausreichend.
Das Schleifen oder Reinigen der Oberfläche war nicht ausreichend.
Die Zwischenschichthaftung zwischen Grund- und Decklackschicht war unzureichend.
- Fehlervermeidung:
- Rost, Fett, Schmutz und Staub von der Oberfläche entfernen.
Die Oberfläche entsprechend dem Material vorbehandeln.
Beim Lackieren auf einer bereits beschichteten Oberfläche, die alte Beschichtung vor dem Auftrag vollständig entfernen.
Die Lackrezeptur entsprechend anpassen.
Zum Auftragen die angegebene Schichtdicke verwenden.
Prüfung der Schichtdicke
Das Messen der Lackschichtdicke ist eine Möglichkeit, um zu überprüfen, ob die Beschichtung entsprechend der Konzeption aufgetragen wurde.
Die Beschichtung soll das Eindringen von Feuchtigkeit und Sauerstoff in das Innere verhindern, um das Trägermaterial vor Korrosion zu schützen. Aus diesem Grund hat die Dicke der Beschichtung einen wesentlichen Einfluss auf die Funktionalität. Das bedeutet jedoch nicht, dass eine dickere Schicht besser ist – die Schichtdicke muss ausreichend sein, damit die Beschichtung ihre volle Funktionalität entfalten kann.
Die Messung der Lackschichtdicke erfolgt mit einem Schichtdickenmessgerät. Es gibt zerstörungsfreie Arten von Schichtdickenmessgeräten, die magnetische Haftfestigkeit und Flussschwankungen zur Messung nutzen, und andere Arten, die Infrarot- und Ultraschallmethoden verwenden.
- Elektromagnetisches Schichtdickenmessgerät:
- Die Schichtdicke kann durch Berühren der Oberfläche mit einer in einen Dauermagneten eingebetteten Sonde gemessen werden. Je nach Stärke der Anziehungskraft des Magneten ändert sich die magnetische Flussdichte. Dieses Messgerät nutzt die Stromänderungen, die durch den Elektromagneten fließen, um die Schichtdicke des Lacks zu messen. Es kann die Dicke der Beschichtung oder Auskleidung (nichtmagnetische Metallschicht, anorganische Schicht oder organische Schicht) auf einem magnetischen Metallsubstrat messen. Das Messprinzip beruht auf dem Prinzip der elektromagnetischen Induktion: Die Beschichtungsdicke wird durch den Magnetfluss gemessen, der von der Sonde durch die nichtmagnetische Beschichtung in das magnetische Trägermaterial unter der Beschichtung fließt. Allerdings kann das elektromagnetische Schichtdickenmessgerät die Dicke einer magnetisch aufgeladenen Lackschicht nicht genau messen.
- Wirbelstrom-Schichtdickenmessgerät:
- Die Schichtdicke wird nach dem Wirbelstromprinzip gemessen. Der Wirbelstrom wird durch einen elektrischen Strom erzeugt, der durch eine Eisenkernspule (Sonde) fließt. Das Messprinzip beruht auf der Proportionalität des Wertes des auf der Metalloberfläche erzeugten Wirbelstroms zum Abstand. Es gibt zwei Arten von Wirbelstrom-Schichtdickenmessgeräten: den kontaktgebundenen Typ, der die Schichtdicke über die Amplitude der Wirbelströme misst, und den berührungslosen Typ, der die Schichtdicke über die Phasendifferenz der Wirbelströme misst. Dieses Messgerät kann für leitfähige, nichtmagnetische Metallsubstrate (wie Aluminium, Kupfer und austenitischer Edelstahl) mit einer Beschichtung aus Kunststoff, Harz, Gummi oder einem anderen isolierenden Material verwendet werden.
- Infrarot-Schichtdickenmessgerät:
- Die Lackschichtdicke kann anhand des Spektrums gemessen werden, das entsteht, wenn die Beschichtung mit Infrarotlicht bestrahlt wird und das durchgelassene oder das reflektierte Licht gestreut wird. Wenn die Beschichtung mit Infrarotlicht bestrahlt wird, kommt es je nach Material und Dicke der Beschichtung zu einer spezifischen Absorption der Lichtwellenlänge. Die Lackschichtdicke des Messobjekts kann anhand des Verhältnisses zwischen der Absorptionsrate und der Dicke des für die Beschichtung verwendeten Materials berechnet werden.
- Ultraschall-Schichtdickenmessgerät:
- Bei Berührung der Sonde mit der Beschichtungsoberfläche sendet der Sensor eine Ultraschallwelle in Richtung des Trägermaterials, wo diese Welle zur Oberfläche zurückreflektiert wird. Anhand der Zeit, die für die Reflexion der Ultraschallwelle benötigt wird, kann die Schichtdicke gemessen werden. Die mit einem Ultraschall-Schichtdickenmessgerät gemessene Schichtdicke wird wie folgt berechnet:
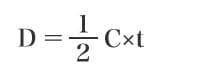
D: Lackschichtdicke
C: Schallgeschwindigkeit in der Beschichtung* (m/s)
t: Gemessene Laufzeit (s)
* Schallgeschwindigkeit in der Beschichtung: Ungefährer Geschwindigkeitswert, der für jedes Material definiert ist. Selbst bei gleichem Material haben verschiedene Typen unterschiedliche Schallgeschwindigkeiten. Aus diesem Grund ist vor dem Einsatz eines Ultraschall-Schichtdickenmessgerätes eine Kalibrierung anhand der tatsächlichen Beschichtung notwendig.
Aktuelle Beispiele für die Messung und Betrachtung von Lackierungen und Beschichtungen
Das Digitalmikroskop der Modellreihe VHX von KEYENCE ermöglicht eine erhebliche Verbesserung der betrieblichen Effizienz und bietet darüber hinaus eine komplexe Betrachtung und Beurteilung von Lackierungen und Beschichtungen mit hochauflösenden Aufnahmen.
Messung der Schichtdicke von Mehrschichtlackierungen mit hochauflösenden optischen Aufnahmen
Das Digitalmikroskop von KEYENCE misst die Lackschichtdicke anhand von optischen Aufnahmen. Dieses Mikroskop wird nicht durch Klarschichten beeinträchtigt, sodass eine scharfe Fokussierung möglich ist. Die Aufnahmen sind klar und bieten umfangreiche Informationen über die Beschichtung.
Schichtdicken, die bisher aufgrund von Fokussierungsfehlern nicht messbar waren, können nun durch die Erfassung des tatsächlichen Beschichtungszustandes genau betrachtet werden.
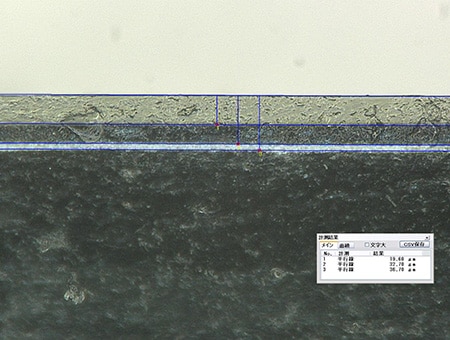
3D-Betrachtung von Klarschichten mithilfe der Fokusansicht- und Multi-Lighting-Funktionen
Dank der verbesserten Bildfrequenz der Kamera kann das VHX durch Verschiebung des motorisierten Objekttisches automatisch den ausgewählten Fokusbereich komplett tiefenscharf anzeigen.
Mit der Kombination aus Tiefenzusammensetzung und Multi-Lighting-Funktion des Digitalmikroskops wird eine tiefenscharfe Aufnahme erstellt und unterschiedliche Beleuchtungsarten automatisch erfasst. Aus diesen Daten kann dann eine geeignete Aufnahme zur Betrachtung ausgewählt werden.
Darüber hinaus ermöglicht der optische Schatteneffekt-Modus – mithilfe der hochauflösenden Objektive, einer 4K-CMOS-Kamera und zugehörigen Beleuchtungstechnologien – eine Überlagerung von Farbinformationen, um Oberflächen- und Echtfarbeninformationen gleichzeitig darzustellen. Dadurch ist eine Profilmessung von kraterförmigen Löchern und anderen Lackierfehlern möglich, wodurch Daten für eine Quantifizierungsanalyse genutzt werden können.
Mit der Betrachtung durch ein Digitalmikroskop, das mit nur einem System sowohl 2D- als auch 3D-Messungen durchführen kann, wird ein neuer Ansatz verfolgt, der den weltweiten Anforderungen an mikroskopische Betrachtungen gerecht wird.
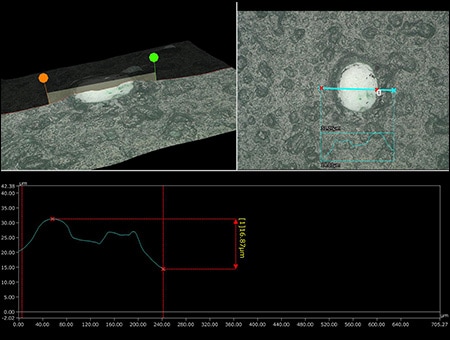
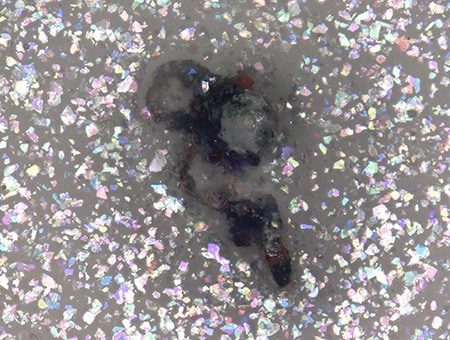
und Tiefenzusammensetzung deutlich abbilden.
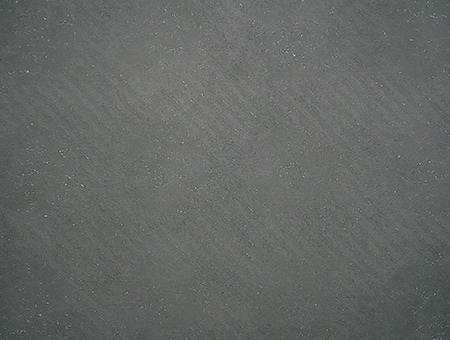
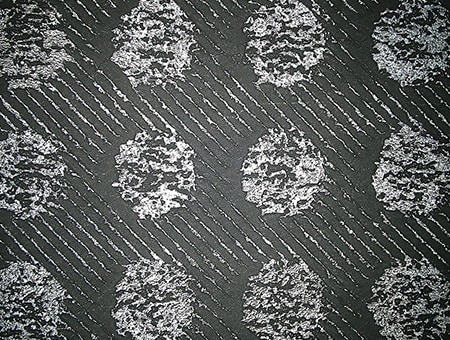
im optischen Schatteneffekt-Modus
Präzise Messung der Pigmentdispersion
Pigmente bestimmen maßgeblich die Funktionalität einer Lackierung. Die Pigmentdispersion kann mit der Modellreihe VHX betrachtet und quantifiziert werden. Pigmente sind feine, lichtechte Farbpartikel, die sich nicht in Wasser oder anderen Lösungsmitteln auflösen. Durch Hinzufügen eines geeigneten Pigments zum Beschichtungsmittel und Mischen dieser Elemente kann eine Beschichtung mit spezifischen Funktionen versehen werden.
Dank der intuitiven Bedienung des Digitalmikroskops können Flächenmessungen und Zählungen innerhalb eines festgelegten Bereichs auf dem Objekt durchgeführt werden. Flächen, die nicht benötigt werden, können ausgeschlossen und überlappende Segmente können getrennt werden. Messergebnisse können als Histogramm ausgegeben werden.
Diese Reihe von Arbeitsschritten ist einfach und erzielt dennoch zuverlässige, präzise Messungen. Anspruchsvolle Analysen können ohne besondere Vorkenntnisse oder Erfahrungen durchgeführt werden.
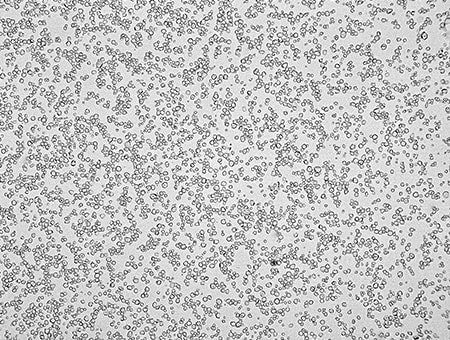
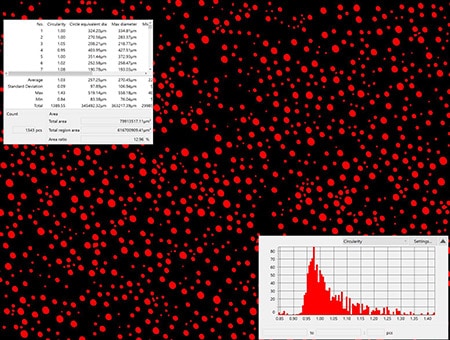
Allgemeine Praktiken für die Messung und Analyse von Lackierungen und Beschichtungen
Das Digitalmikroskop der Modellreihe VHX bietet eine hervorragende Effizienz und ermöglicht es, anwenderabhängige Schwankungen zu vermeiden und eine genaue Messung und Analyse sicherzustellen.
Die hochauflösenden Aufnahmen, die durch modernste optische Bildverarbeitungs- und Automatisierungstechniken erzeugt werden, ermöglichen eine detaillierte und klare Betrachtung von Beschichtungen, Lackierfehlern und Dispersionen. Die Einfachheit dieser Analyse-Tools ermöglicht es selbst unerfahrenen Anwendern, sehr genaue Analyseergebnisse zu erlangen.
Die erfassten bzw. gemessenen Daten können mit der Berichtsfunktion einfach als Bericht mit einem festen Format ausgegeben werden. Die gemeinsame Nutzung dieser Daten über einen Intranet-Server ist nicht nur für die Qualitätssicherung und die Gewährleistung der Konformität gemäß Industriestandards nützlich, sondern auch für die Ursachenanalyse von Lackierfehlern sowie für die Prozessoptimierung.
Dank einer Vielzahl an erweiterten Messfunktionen ist die Modellreihe VHX ein leistungsstarker Partner für die Gewährleistung der Qualität und Zuverlässigkeit von Lackierungen und Beschichtungen.
Für weitere Informationen klicken Sie bitte auf die unten angezeigte Schaltfläche, um die Broschüre herunterzuladen. Für Anfragen klicken Sie bitte auf die entsprechende Schaltfläche, um KEYENCE zu kontaktieren.