Betrachtung und Messung von Sinterteilen mit einem Digitalmikroskop
Zur Herstellung von Sinterteilen werden metallische oder keramische Pulver in Metallformen gepresst. Diese Formteile werden dann bei Temperaturen unterhalb ihres Schmelzpunktes gebrannt und gehärtet. Die Vorteile des Sinterns liegen darin, dass nur eine geringe Energiemenge bei minimalen Materialverlusten benötigt wird und kein Aufwand für die sekundäre Verarbeitung erforderlich ist, da die Metalle nicht geschmolzen werden müssen. Dieser Abschnitt gibt einen Überblick über das Sintern und stellt Beispiele für die Betrachtung und Messung von Sinterteilen mit einem Digitalmikroskop vor.
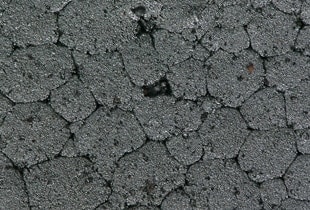
- Vor- und Nachteile des Sinterns
- Prinzip des Sinterns
- Ablauf des Sinterns
- Beispiele für die Betrachtung und Messung von Sinterteilen mit einem Digitalmikroskop
Vor- und Nachteile des Sinterns
Sintern eignet sich zur Herstellung verschiedenster Teile, da die Materialien nicht geschmolzen werden müssen.
- Vorteile des Sinterns
-
- Fast jedes Material kann verwendet werden, solange es sich pulverisieren lässt.
- Eine sekundäre Verarbeitung ist in vielen Fällen nicht erforderlich.
- Die Materialverluste sind gering.
- Komplexe Formen können geformt werden.
- Die Materialien können beliebig gemischt werden.
- Sinterteile sind porös und daher leicht.
- Selbst Materialien mit hohem Schmelzpunkt können verarbeitet werden.
- Nachteile des Sinterns
-
- Es werden Pulver verarbeitet, was die Materialkosten erhöht.
- Teile schrumpfen, wenn sie gesintert werden.
- Die mechanischen Eigenschaften, wie z. B. die Festigkeit, sind schlechter als die, die durch Gießen oder Pressen hergestellt werden.
Prinzip des Sinterns
Feste Pulveroberflächen sind instabil, weil die Atome, Moleküle und Ionen nicht miteinander verbunden sind. Wenn feste Pulver erhitzt werden, bilden sich Verbindungen, so genannte Hälse. Wenn sich Atome, Moleküle und Ionen von der Oberfläche der Pulverpartikel zu den Hälsen bewegen (diffundieren), werden die Hälse größer und die Oberfläche nimmt ab. Während die Hälse in den Anfangs-, Zwischen- und Endstadien weiter wachsen, nimmt die Dichte zu und der Sintervorgang ist abgeschlossen.
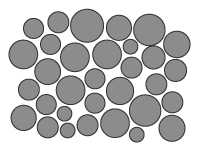
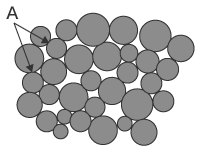
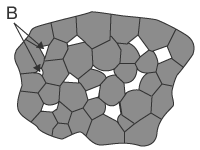

- A: Hals
- B: Offene Poren
- C: Geschlossene Poren
Poren, die mit der Außenluft verbunden sind, werden als offene Poren bezeichnet, während die in einem Objekt isolierten Poren als geschlossene Poren bezeichnet werden.
Ablauf des Sinterns
- Mischungsverhältnisse der Materialien in Pulverform bestimmen und mischen, bis eine gleichmäßige Mischung entsteht.
- Pulvermischung in eine Metallform geben und in einer Presse formen.
- Formteil mehrere Stunden lang in einem Sinterofen erhitzen.
Die Materialpulver schmelzen nicht, da das Formteil bei einer Temperatur unterhalb ihres Schmelzpunktes ausgehärtet wird. Materialpulver werden bei längerer Erhitzung fest miteinander verbunden und das Sinterteil entsteht.
Die Sinteröfen sind mit Gasen gefüllt, um zu verhindern, dass das gesinterte Teil oxidiert.
Die gesinterten Teile können geschliffen oder poliert werden, um die Genauigkeit zu erhöhen, oder wärmebehandelt werden, um die Härte zu erhöhen.
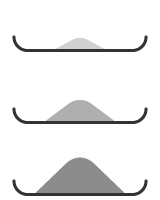
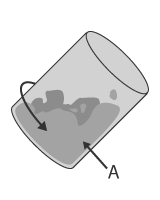
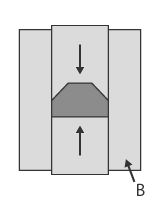
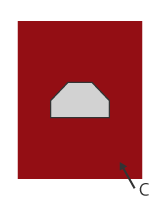
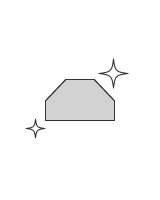
- A: Mixer
- B: Presse
- C: Sinterofen
Beispiele für die Betrachtung und Messung von Sinterteilen mit einem Digitalmikroskop
Im Folgenden werden die neuesten Beispiele für die Betrachtung und Messung von Sinterteilen mithilfe eines Digitalmikroskops der Modellreihe VHX von KEYENCE vorgestellt.

Geringe Dichte der Partikelgrenzflächen (geringe Festigkeit)
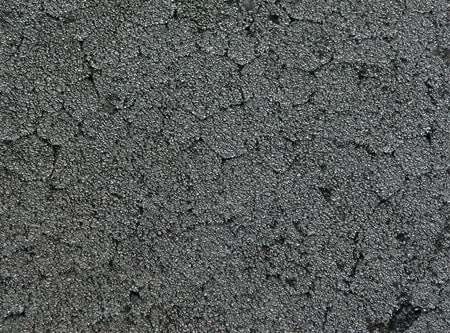
Hohe Dichte der Partikelgrenzflächen (hohe Festigkeit)
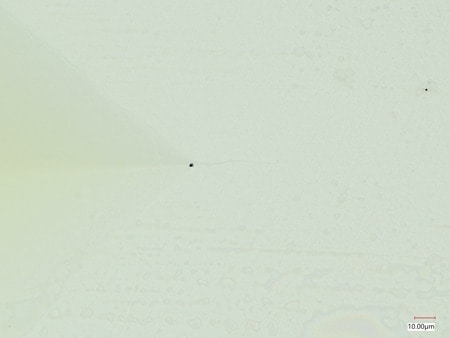
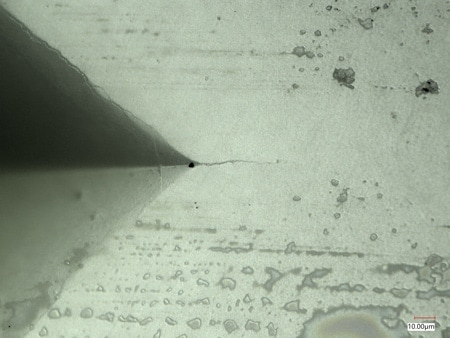
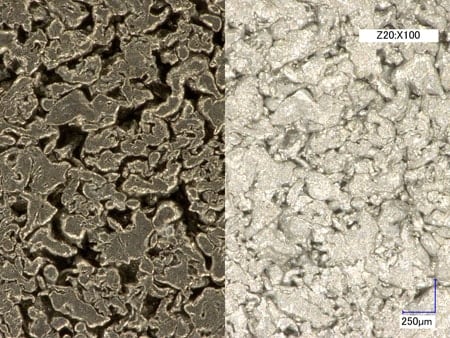
Links: Mit Aufsatz. Rechts: Ohne Aufsatz
Die Verwendung des einstellbaren Beleuchtungsaufsatzes ermöglicht eine klare Betrachtung der Poren.
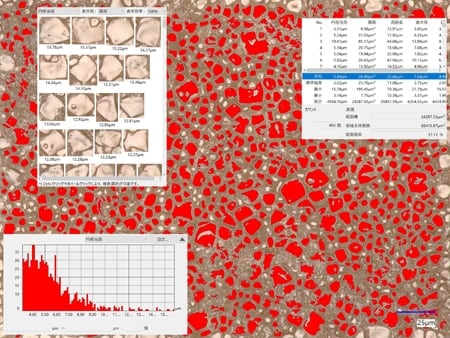
Durch die Möglichkeit der automatischen Flächenmessung können die Körner schnell und präzise gezählt werden.
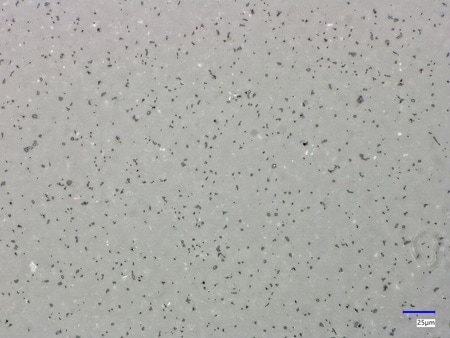
Vor der Messung
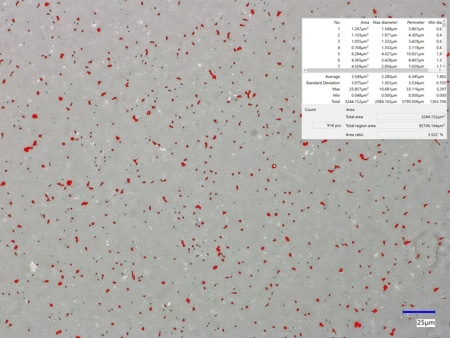
Automatische Flächenmessung
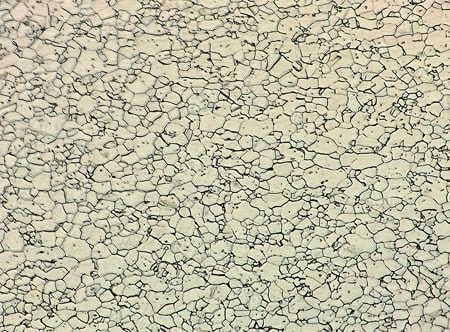
Vor der Messung
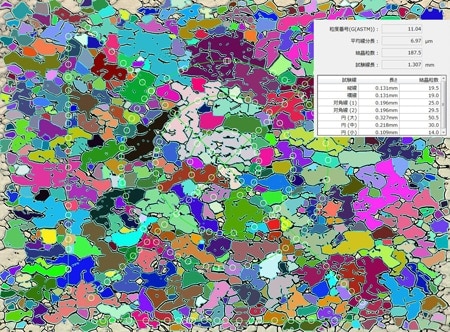
Automatische Flächenmessung (Korngrößenanalyse)
Die automatische Flächenmessung ermöglicht eine Korngrößenanalyse, wodurch sich der Arbeitsaufwand für die Analyse erheblich verringert.