Probleme und Optimierung der Messung in der Maschine
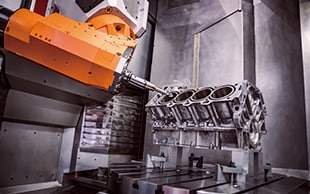
Bei der Herstellung von großformatigen Produkten ist die Messung in der Maschine so wichtig, dass sie als Geheimwaffe für Optimierungen wie die Verbesserung der Schnittqualität und die Beseitigung von Abfällen in den Prozessen angesehen wird. Die Messung in der Maschine wird jedoch auf Werkzeugmaschinen wie fünfachsigen Werkzeugmaschinen, Fünf-Seiten-Fräsmaschinen und Drehmaschinen durchgeführt, sodass sich die für die Messung benötigte Zeit direkt auf die Betriebsrate auswirkt. Daher muss die Messung in der Maschine in möglichst kurzer Zeit erfolgen.
In diesem Abschnitt werden die Vorteile, Nachteile und Messpunkte der Messung in der Maschine bei der Herstellung von großformatigen Produkten (die kurze Lieferzeiten und verbesserte Qualität erfordern) sowie die mit diesen Messungen verbundenen Probleme erläutert. Außerdem werden Beispiellösungen für Messprobleme mit unserem neuesten 3D-Koordinatenmessgerät vorgestellt, einem Gerät, das für die Optimierung der Messung in der Maschine unerlässlich ist.
- Was ist eine Messung in der Maschine?
- Vorteile und Nachteile einer Messung in der Maschine
- Punkte für die Messung in der Maschine
- Probleme der Messung in der Maschine und ihre Lösungen
- Positionierung und Messung der Bearbeitungszugabe auf einer Fünf-Seiten-Fräsmaschine
- Messung des Innendurchmessers, der Ebenheit und der Rechtwinkligkeit eines großen Flansches auf einer Vertikaldrehmaschine (Drehbank)
- Messung des Lochabstands, des Lochdurchmessers und der Position auf einem Horizontalbohrwerk
- Optimierung der Messung in der Maschine
Was ist eine Messung in der Maschine?
Die Messung in der Maschine bezieht sich auf die Messung der Formen eines Produkts, während es sich noch in einer Werkzeugmaschine befindet. Dies gilt nicht nur für Drehmaschinen, Fräsmaschinen und allgemeine Drehzentren, sondern auch für Werkzeugmaschinen wie fünfachsige Werkzeugmaschinen und Fünf-Seiten-Fräsmaschinen. Die Bediener messen das zu bearbeitende Produkt, ohne es aus dem Werkzeug nehmen zu müssen.
Durch die Messung der Abmessungen eines Produkts auf einer Werkzeugmaschine entfällt die Arbeit des Positionierens und Ausrichtens der Welle des Produkts, die durchgeführt werden muss, wenn das Produkt entnommen und wieder auf die Werkzeugmaschine gesetzt wird, und ermöglicht eine Feineinstellung der Genauigkeit durch zusätzliche Bearbeitung.
Die internationale Norm ISO 230 schreibt die Prüfmethodik von Werkzeugmaschinen für die Messung in der Maschine vor, wie z. B. Prüfungen der Positioniergenauigkeit über die numerische Steuerung, Prüfungen der geometrischen Genauigkeit für die Drehachse und Prüfungen der diagonalen Positioniergenauigkeit.
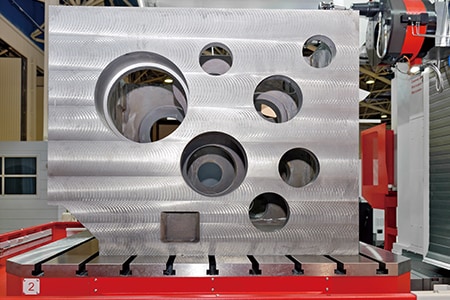

Vorteile und Nachteile einer Messung in der Maschine
Bei den normalen Maßprüfungen von Fertigungsprozessen wird die Bearbeitungsgenauigkeit (z. B. die Abmessungen von bearbeiteten Produkten) gemessen. Produkte außerhalb der Toleranzen werden als fehlerhaft eingestuft. Bei der Messung in der Maschine wird jedoch die Bearbeitungsgenauigkeit der zu bearbeitenden Produkte während des Bearbeitungsprozesses auf den Werkzeugmaschinen gemessen.
In diesem Abschnitt werden die Vor- und Nachteile der Messung in der Maschine vorgestellt, die durch die Messung von Maßen erzielt wird, ohne dass die Produkte aus den Werkzeugmaschinen entfernt werden.
Vorteile
Zu den Vorteilen der Messung in der Maschine gehören die Verbesserung der Bearbeitungsqualität und die Vermeidung von überflüssigen Transport- und Messtätigkeiten. Diese Vorteile führen zu kürzeren Arbeitszeiten und einer geringeren Belastung der Mitarbeiter.
Verhindert die Freigabe von fehlerhaften Produkten für den nächsten Prozess
Bei der normalen Messung werden die Messungen im Rahmen des Prüfprozesses durchgeführt. Anschließend werden zusätzliche Bearbeitungen und ähnliche Operationen vorgenommen. Bei der Messung in der Maschine werden die Produkte jedoch während der Bearbeitung gemessen und anschließend weiterverarbeitet. Die Bearbeitungsgenauigkeit wird während des Bearbeitungsprozesses überprüft. Anschließend werden Feinkorrekturen an der Genauigkeit mit zusätzlichen Bearbeitungen vorgenommen, um zu verhindern, dass fehlerhafte Produkte in den nächsten Prozess gelangen.
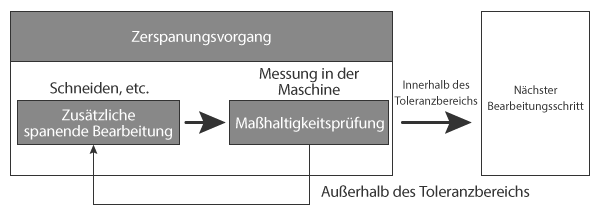
Eliminiert überflüssige Transportvorgänge
In einer Produktionsstätte gibt es sieben Schwundbereiche, die im Auge behalten werden sollten. Einer davon sind überflüssige Transportvorgänge. Transportverschwendung bezieht sich auf unnötige Transportvorgänge. Durch die Messung in der Maschine (bei der die Abmessungen von Produkten auf Werkzeugmaschinen gemessen werden) entfällt der Aufwand für die Entnahme der Produkte aus den Werkzeugmaschinen und den Transport ins Messlabor sowie der Rücktransport der Produkte zu den Werkzeugmaschinen nach der Messung. Mit dieser Methode der Messung entfällt auch der Zeitverlust, der durch das Warten auf die Verfügbarkeit von Messgeräten im Messlabor entsteht.
Eliminiert überflüssige Messvorgänge
Die Messung in der Maschine eliminiert auch überflüssige Bewegungen, die die für die Messung erforderliche Positionierung und Ursprungsbestimmung anzeigen. Bei der Messung in der Maschine wird der Bearbeitungsursprung verwendet, sodass die für die Messung erforderliche Positionierung und Ursprungsbestimmung nicht erforderlich ist und entsprechende überflüssige Bewegungen entfallen.
Nachteile
Zu den Nachteilen gehören die verringerte Auslastung der Werkzeugmaschinen aufgrund der Maßhaltigkeitsprüfung mit diesen Werkzeugen, der Aufwand für die Erstellung von Messprogrammen und die Messgenauigkeit.
Verringertes Arbeitstempo der Werkzeugmaschine
Wenn die Messung in der Maschine lange dauert, kann dies zu einer Senkung der Betriebsrate der Werkzeugmaschine führen. Für Messungen mit Handmessmitteln wie Messschiebern, Messuhren und Dickenmessgeräten sind mehrere Mitarbeiter erforderlich. Zudem sind diese Messungen bei zahlreichen Messpunkten sehr zeit- und arbeitsaufwändig. Daher müssen bei der Messung in der Maschine effiziente Messgeräte verwendet werden, die die Messzeit so weit wie möglich verkürzen können.
Laden der Messprogrammerstellung
In den letzten Jahren wurden Werkzeugmaschinen entwickelt, die mit maschineninternen Messfunktionen ausgestattet sind. Es müssen jedoch Programme erstellt werden, um diese Messung durchzuführen.
Diese Aufgabe erfordert eine spezielle Software. Auch wenn die optionalen Funktionen der 3D-CAD-Software genutzt werden, sind ein hohes Maß an Bearbeitungskenntnissen und Programmierfähigkeiten erforderlich. Außerdem müssen neue Programme erstellt werden, um neue Produkte zu messen, sodass mehrere Produkttypen in kleinen Losen eine große Belastung für den Programmierer darstellen.
Messgenauigkeit
Bei der Messung mit maschineninternen Messfunktionen von Werkzeugmaschinen treten Fehler aufgrund von Faktoren wie beispielsweise dem Spiel der Antriebseinheit auf, das ein Problem darstellt. Da außerdem das Antriebssystem der Werkzeugmaschine selbst zur Durchführung der Messung verwendet wird, kann man nicht von einer objektiven Messung im eigentlichen Sinne sprechen. Dies stellt ein grundlegendes Problem dar.
In den letzten Jahren wurden Koordinatenmessgeräte entwickelt, die die oben genannten Nachteile reduzieren und die Vorteile der Messung in der Maschine nutzen können.
Punkte für die Messung in der Maschine
Die Messung in der Maschine wird auf verschiedenen Werkzeugmaschinen durchgeführt. In diesem Abschnitt werden die Messungen erläutert, die bei der Bearbeitung mit Fünf-Seiten-Fräsmaschinen, Vertikaldrehmaschinen und Horizontalbohrwerken zu beachten sind.
Fünf-Seiten-Fräsmaschinen: Positionierung und Bearbeitungszugabe

Fünf-Seiten-Fräsmaschinen werden für die Bearbeitung von Produkten eingesetzt, die Anforderungen wie komplizierte Formen, Abmessungen von ±0,01 mm und genaue Parallelität und Ebenheit erfüllen müssen. Bei diesen Maschinen bleibt das Produkt stationär. Die Oberflächen vorn, hinten, links, rechts und oben werden durch den beweglichen Werkzeugachsenanschluss bearbeitet.
Es liegt in der Natur der Sache, dass Fünf-Seiten-Fräsmaschinen mit höherer Genauigkeit arbeiten können als dreiachsige Werkzeugmaschinen. Da sich die Werkzeugachse jedoch in komplizierten Mustern durch viele Bearbeitungsachsen bewegt, können Fehler in der Produktpositionierung bei einer Fünf-Seiten-Fräsmaschine größere Bearbeitungsfehler verursachen als bei einer dreiachsigen Werkzeugmaschine.
Die Bearbeitungszugabe zeigt den Teil des Materials an, der abgeschnitten wird. Sie zeigt den Teil an, der über die Fertigmaße hinaus abgetragen wird, wie der Teil, der bei der Endbearbeitung der Materialoberfläche durch Abheben abgetrennt wird. Ein Verständnis für die Höhe der Bearbeitungszugabe macht es also einfach, Fehler während der Bearbeitung zu erkennen. Wenn mehr Material abgeschnitten wird, als die Maschine zulässt, muss das Produkt entsorgt werden. Daher muss dieser Punkt vor der Bearbeitung gemessen werden.
Vertikaldrehmaschinen (Drehbänke): Wellenausrichtung
Im Allgemeinen werden unter den Großdrehmaschinen Vertikaldrehmaschinen verwendet, um besonders große Produkte zu drehen. Sie werden auch als Drehbänke bezeichnet. Das Produkt wird auf einen Drehtisch wie eine Töpferscheibe mit einer Drehachse in vertikaler Richtung gesetzt und gedreht. Das Eigengewicht des Produkts sichert es auf dem Drehtisch, sodass große, runde Produkte stabil gedreht und auf der Drehmaschine bearbeitet werden können. Außerdem führen Schwerkraft und Zentrifugalkraft zu einem geringeren Rundlauf als bei einer Horizontaldrehmaschine, was eine hohe Drehgenauigkeit ermöglicht. Vertikaldrehmaschinen können leicht an Planscheiben befestigt werden, sodass sie die Bearbeitung von dünnen Ringen mit hohen Genauigkeitsanforderungen unterstützen.
Vertikaldrehmaschinen haben diese Vorteile, erfordern aber eine Ausrichtung der Welle, da die Referenz zurückgesetzt wird, wenn das Produkt aus dem Futter genommen wird. Wird eine weitere Bearbeitung vorgenommen, müssen daher Messungen durchgeführt werden, um zu bestätigen, dass die Welle in der gleichen Position wie bei der vorherigen Bearbeitung ausgerichtet wurde.
Horizontalbohrwerke: Lochabstand, Lochdurchmesser und Position
Ein Horizontalbohrwerk ist ein Bohrwerk, dessen Schneidwerkzeug eine horizontale Drehachse hat. Es kann mehr Späne auswerfen als Vertikalbohrwerken und kann daher größere und tiefere Löcher bearbeiten. Außerdem bewegt sich die Drehachse des Schneidewerkzeugs, um das Messobjekt zu bearbeiten, sodass das Produkt nicht bewegt werden muss, was sich für die Herstellung von großformatigen Produkten eignet.
Horizontalbohrwerke haben diese Vorteile, aber die Referenz wird zurückgesetzt, wenn das Produkt aus dem Spannfutter genommen wird. Daher ist es bei der Positionierung vor der Bearbeitung oder bei der Durchführung zusätzlicher Bearbeitungen unerlässlich, Messungen durchzuführen, um zu bestätigen, dass sich das Produkt in der gleichen Position befindet und dass die Wellenausrichtung abgeschlossen ist.
Probleme der Messung in der Maschine und ihre Lösungen
Es ist wichtig, den Verarbeitungsstatus von großformatigen Produkten nicht nur nach, sondern auch während der Herstellung zu überprüfen. Üblicherweise werden diese Messungen mit Handmessmitteln wie Messschiebern, Messuhren und Dickenmessgeräten durchgeführt. Um dreidimensionale Formen zu messen, müssen die Produkte in ein Messlabor gebracht werden. Messung, Transport und die Einstellung der Produkte auf den Werkzeugmaschinen nahmen jedoch viel Zeit in Anspruch, was zu längeren Zeiträumen bis zur Auslieferung und Inbetriebnahme führte.
Um diese Probleme zu lösen, werden in immer mehr Fällen die neuesten 3D-Koordinatenmessgeräte (KMG) eingesetzt.
Das Mobile 3D-Koordinatenmessgerät der Modellreihe WM von KEYENCE ermöglicht die hochpräzise Messung von großformatigen Produkten auf Werkzeugmaschinen mit dem kabellosen Messtaster, wodurch sie sich für die Messung in der Maschine eignet. Selbst vertiefte Bereiche von Messobjekten können ohne Bewegungseinschränkungen innerhalb des Messbereichs erreicht werden, was Messungen durch eine einzelne Person ermöglicht, die das Messobjekt einfach mit dem Messtaster antasten kann. Außerdem variieren die Messergebnisse im Gegensatz zu Handmessmitteln nicht, was eine quantitative Messung ermöglicht.


Positionierung und Messung der Bearbeitungszugabe auf einer Fünf-Seiten-Fräsmaschine
Um ein Portal-Koordinatenmessgerät (CMM) zur Messung eines großformatigen Produkts zu verwenden, das mit einer Fünf-Seiten-Fräsmaschine bearbeitet wurde, muss das Produkt aus der Fünf-Seiten-Fräsmaschine entfernt und in das Messlabor gebracht werden. Das ist eine schwierige Arbeit, für die viel Personal erforderlich ist. Selbst die Messung in der Maschine mit Handmessmitteln erfordert mehrere Mitarbeiter und nimmt sehr viel Zeit in Anspruch, was die Auslastung der Fünf-Seiten-Fräsmaschine verringert. Das stellt ein Problem dar.
Wenn diese Produkte zusätzlich bearbeitet werden, während die endgültige Genauigkeit überprüft wird, ist es außerdem besser, ihre Maße auf Fünf-Seiten-Fräsmaschinen zu messen, anstatt sie zu entfernen. Daher kann man sagen, dass für die Maßhaltigkeitsprüfung großformatiger Produkte der Einsatz eines Koordinatenmessgeräts ideal ist, das kompakt und tragbar ist und eine große Fläche eines Produkts auf einer Fünf-Seiten-Fräsmaschine messen kann.
Die Modellreihe WM ermöglicht die 3D-Messung großformatiger Produkte durch eine Person, ohne dass diese von den Fräsmaschinen entfernt werden müssen. Der kabellose Messtaster erleichtert die Positionierung, da die Referenzfläche des Produkts vor der Bearbeitung und der Bearbeitungsursprung genau gemessen werden können. Der Zeitaufwand für die Arbeit vor den Messungen kann erheblich reduziert werden.
Auch die Messung von Formen einschließlich der Bearbeitungszugabe vor der Bearbeitung und die Kompensation von Bearbeitungsfehlern verbessert die Effizienz der Bearbeitungsarbeiten für die Feineinstellung am Ende des Prozesses. Darüber hinaus können Prüfberichte mit Fotos der Messpunkte vor Ort erstellt werden, so dass die Genauigkeit mit hoher Zuverlässigkeit vor der Produktauslieferung garantiert werden kann.




Messung des Innendurchmessers, der Ebenheit und der Rechtwinkligkeit eines großen Flansches auf einer Vertikaldrehmaschine (Drehbank)
Die Positionen der Bolzenlöcher zur Befestigung von Trägermaterialien und Flanschen an einem Druckbehälter sind wichtige Messungen, die die Festigkeit und Stabilität nach der Installation beeinflussen. Daher müssen Innendurchmesser, Ebenheit und Rechtwinkligkeit der Flansche nicht nur während der Herstellung, sondern auch bei der Auslieferung des Druckbehälters gemessen werden.
Für die Durchführung dieser Messungen mit Handmessmitteln sind mehrere Mitarbeiter erforderlich. Außerdem können einige Elemente von Bolzen, die sich auf der Rückseite befinden, wie z. B. der mittlere Durchmesser eines Bolzenlochs, nicht gemessen werden, da sie durch andere Teile blockiert werden. Selbst wenn sie gemessen werden können, können die gemessenen Werte instabil sein, was einen Vergleich mit den Auslegungswerten erschwert.
Mit der Modellreihe WM ist es möglich, dass eine einzelne Person quantitative Messungen durch einfaches Antasten der Messpunkte mit dem Messtaster durchführen kann. Mit dem kabellosen Messtaster gibt es keine Bewegungseinschränkungen, wodurch die Messung von vertieften Bereichen von Messobjekten ermöglicht wird. Die Bediener können sogar Innendurchmesser, Ebenheit und Rechtwinkligkeit eines Flansches messen, indem die Messpunkte einfach mit dem Messtaster angetastet werden. Es können sogar 3D-Positionskoordinaten gemessen werden.
Darüber hinaus ist die Modellreihe WM tragbar und erfüllt damit die Anforderung, die 3D-Arbeitsgenauigkeit vor Ort zu messen, was mit herkömmlichen 3D-Koordinatenmessgeräten (KMG) nicht möglich ist.




Messung des Lochabstands, des Lochdurchmessers und der Position auf einem Horizontalbohrwerk
Die genaue Prüfung von Steigung, Durchmesser und Position der Gewindebohrungen, die zur Verbindung von Flanschen (die mit Horizontalbohrwerken bearbeitet werden) mit anderen Teilen verwendet werden, ist notwendig, da die Genauigkeit dieser Maße die Festigkeit der Verbindungen stark beeinflusst. Die Bediener messen den Lochabstand und den Durchmesser mit einem Maßband oder Messschieber. Es müssen jedoch viele Punkte gemessen werden, so dass mindestens zwei Personen und viel Zeit erforderlich sind, um diese Elemente mit Handmessmitteln zu messen. Außerdem sind Positionsmessungen mit Handmessmitteln schwierig durchzuführen, da der Abstand zum Nullpunkt gemessen werden muss. Für die Messung mit einem Portal-Koordinatenmessgerät (KMG) muss das Produkt aus dem Horizontalbohrwerk genommen und in das Messlabor gebracht werden. Das ist eine schwierige Arbeit, für die viel Personal erforderlich ist. Außerdem sind Positionierungs- und andere Einstellungen erforderlich, wenn das Produkt zur weiteren Bearbeitung wieder in das Horizontalbohrwerk eingelegt wird.
Mit der Modellreihe WM kann Lochabstand, Durchmesser und Position ganz einfach bestimmt werden, indem der kabellose Messtaster auf den zu messenden Oberflächen angebracht wird. Das Produkt muss nicht aus dem Horizontalbohrwerk entfernt werden. Darüber hinaus können neben einfachen linearen Abständen auch 3D-Elemente wie Diagonalen und Ebenenwinkel gemessen werden. Die Modellreihe WM ermöglicht auch die Vergleichsmessung von Messobjekten und Formen, die aus einer 3D-CAD-Datei importiert wurden, und die Ausgabe der Messergebnisse als CAD-Daten.




Optimierung der Messung in der Maschine
Die Modellreihe WM ermöglicht Messungen in der Maschine an verschiedenen Werkzeugmaschinen durch einfaches Antasten von Messobjekten mit dem kabellosen Messtaster. Zusätzlich zu den oben vorgestellten Leistungsmerkmalen bietet die Modellreihe WM folgende Vorteile:

- Hochpräzise Messung über einen großen Bereich
- Ein großer Messbereich bis zu 15 m kann mit hoher Genauigkeit gemessen werden. Die Modellreihe WM ist mit dem Navigationsmessmodus ausgestattet, der die Messung am selben Punkt nach einem gespeicherten Messverfahren ermöglicht, sodass jeder die gleichen Messdaten erhalten kann.

- Augmented Reality als Orientierungshilfe
- Bilddaten von gemessenen Messobjekten können als Messverfahren gespeichert werden. Diese Verfahren können zur OK/NG-Beurteilung bei der Messung mehrerer Messobjekte derselben Form verwendet werden, indem Sie einfach die Anweisungen auf dem Bildschirm befolgen und den Messtaster an das Messobjekt halten.

- Statistische Auswertungsfunktion zur Zusammenfassung der Messergebnisse
- Messergebnisse von geführten Messungen werden automatisch auf der Festplatte gespeichert. Die gespeicherten Daten können dann für verschiedene statistische Analysen extrahiert werden, z. B. für die Überprüfung der statistischen Werte, Trendgrafiken und Histogramme.

- Leicht verständliche Schnittstelle
- 3D-Koordinatenmessgeräte arbeiten oft mit komplizierten und ungewohnten Befehlen. Die Modellreihe WM bietet eine intuitive Bedienung mit Bildern und Symbolen, wodurch das System leicht bedient werden kann.
Die Modellreihe WM unterstützt in hohem Maße die Analyse, wie z. B. den Vergleich mit 3D-CAD-Daten, sowie die Messung der Abmessungen und Formen während der Messung in der Maschine. Sie verbessert die Effizienz der Herstellung von verschiedenen Dreh- und Frästeile und der für das Einrichten und Qualitätsmanagement erforderlichen Arbeiten erheblich.